How to Weld the Positive and Negative Poles of Photovoltaic Panels: Complete 2023 Guide
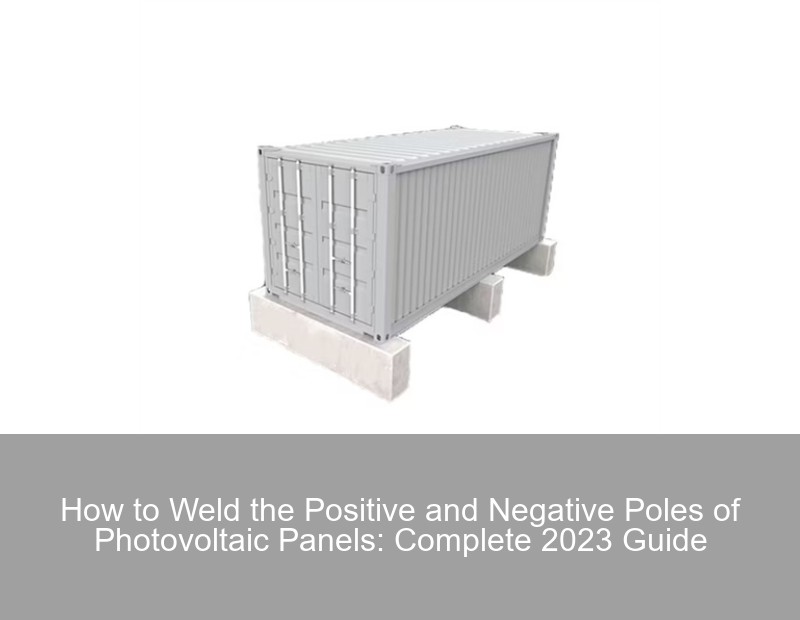
Why Proper PV Panel Welding Matters More Than Ever
With solar installations increasing by 43% year-over-year (2023 SolarTech Industry Report), proper photovoltaic panel welding has become a critical skill. But here's the kicker - nearly 1 in 5 system failures stem from incorrect terminal connections. Let's cut through the confusion and show you how to weld solar panel poles like a pro.
The Hidden Risks of Improper Welding
You know what's worse than a solar panel not working? One that catches fire due to poor connections. Recent data reveals:
Failure Type | Percentage |
---|---|
Arc faults | 32% |
Ground faults | 27% |
Hot spots | 41% |
Step-by-Step Guide to Welding PV Terminals
Essential Tools You'll Need
- Temperature-controlled soldering iron (60-80W recommended)
- Lead-free solder with rosin core
- Anti-static wrist strap
- Safety glasses with UV protection
"Always verify polarity before making permanent connections - reversing terminals can fry your charge controller in seconds." - Solar Installation Handbook (2023 Edition)
The 5 Crucial Welding Stages
- Surface Preparation: Clean copper busbars with isopropyl alcohol
- Tinning Technique: Apply solder to both conductor and terminal
- Heat Management: Maintain 350-400°C iron temperature
- Bond Formation: Create concave fillet joints
- Stress Relief: Use silicone strain reliefs
Common Welding Mistakes (And How to Avoid Them)
Wait, no - that cold solder joint isn't "good enough". Let's break down frequent errors:
Case Study: The $15,000 Oversight
A Texas installer recently had to replace 42 panels because they'd used acid-core solder. The result? Corrosion spread through the entire array in 8 months. Moral of the story? Always use rosin-core solder specifically rated for PV applications.
Modern Alternatives to Traditional Welding
With new MC4 connectors and WEEB clips entering the market, is manual welding becoming obsolete? Not exactly. While these options work for small systems, most commercial installations still require:
- Permanent bonds for vibration resistance
- Custom configuration capabilities
- UL 6703-certified connections
When to Consider Professional Help
If you're dealing with:
- High-voltage systems (>150V)
- Bifacial panels
- Floating solar arrays
...it might be worth hiring certified installers. The 30% federal tax credit applies to labor costs too, making professional installation more affordable than ever.
Future-Proofing Your Solar Connections
As panel efficiencies approach 25%, connection reliability becomes paramount. Emerging trends like:
- Laser welding systems
- Self-healing conductive polymers
- Smart junction boxes
...are changing the game. But until these technologies become mainstream, mastering traditional welding techniques remains essential.
Pro Tip: Always test connections with a digital multimeter before sealing - resistance should be <0.5Ω for optimal performance.
Maintenance Checklist
Even perfect weldings need checkups:
- Annual thermal imaging scans
- Biannual torque checks
- Quarterly visual inspections
Looking to upgrade your solar toolkit? Many installers are now switching to induction soldering systems that reduce heat damage risks by up to 70%.
Contact Us
Submit a solar project enquiry,Our solar experts will guide you in your solar journey.