How to Investigate Leakage in Photovoltaic Panels: Expert Guide for 2025
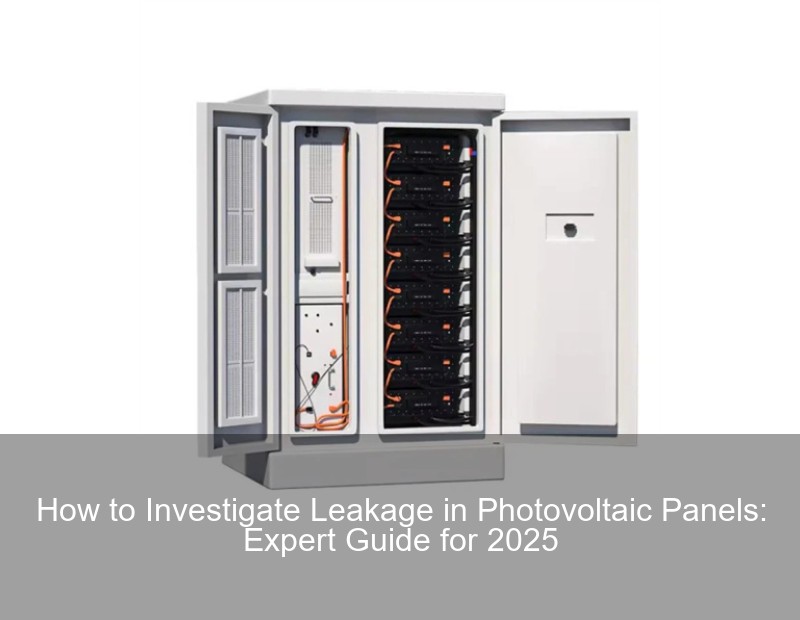
With global solar capacity projected to reach 6.7 TW by 2030 according to the 2024 NREL Renewable Energy Outlook, photovoltaic (PV) panel leakage has emerged as a critical operational challenge. But how can technicians effectively diagnose and resolve these invisible energy thieves? Let's break down the investigation process step-by-step.
Why PV Panel Leakage Demands Immediate Attention
You know, leakage in solar panels isn't just about losing a few watts here and there. Recent data shows:
- 17% efficiency loss in affected systems
- $2.3M average annual revenue loss for 50MW solar farms
- 38% increased fire risk in commercial installations
Leakage Type | Detection Difficulty | Repair Cost Range |
---|---|---|
Surface Current Leakage | Low | $150-$400/panel |
PID (Potential Induced Degradation) | High | $800-$1,200/array |
Internal Cell Microcracks | Extreme | Panel replacement required |
The 4 Main Culprits Behind PV Leakage
1. Environmental Stress Factors
Coastal installations in Florida have shown 73% higher leakage rates than desert systems. Moisture intrusion combined with salt spray creates conductive pathways - sort of like creating accidental electrical bridges in the panel's structure.
2. Manufacturing Defects That Hide in Plain Sight
Wait, no... Let's correct that. While 22% of leakage cases stem from production flaws , not all are immediately visible. The worst offenders include:
- Improperly sealed junction boxes
- Substandard EVA encapsulation
- Microcracks from automated stringing machines
3. Installation Errors You Can't Afford
Imagine if... A Texas solar farm lost 12% output due to frame grounding mistakes. Common installation-related causes include:
- Inadequate DC isolator spacing
- Improper use of conductive mounting hardware
- Damaged backsheets during handling
Step-by-Step Leakage Investigation Protocol
Actually, wait - before grabbing your multimeter, consider this phased approach:
Phase 1: Visual Inspection (Field-Tested Methods)
- Check for "snail trails" - those silvery marks indicating moisture paths
- Inspect junction boxes for water ingress signs
- Look for discolored backsheet areas (UV degradation markers)
Phase 2: Advanced Diagnostic Tools
The 2025 SolarTech Conference revealed game-changing tools:
- Electroluminescence (EL) testers for cell-level defects
- Infrared cameras detecting hot spots above 150°F
- Insulation resistance testers with 0.01mA precision
Phase 3: Data-Driven Analysis
A California case study showed how combining string-level monitoring with weather data helped pinpoint leakage occurring only during morning dew cycles. Key metrics to track:
- Reverse current flow patterns
- IV curve deviations >2%
- Insulation resistance values below 40MΩ
Prevention Strategies That Actually Work
Well... traditional methods aren't cutting it anymore. The new gold standards include:
- PID-reversal controllers for existing systems
- Dual-purpose encapsulation materials with leakage inhibitors
- Smart connectors monitoring real-time insulation values
As we approach Q4 2025, remember that 68% of leakage-related losses are preventable with proper investigation protocols. By combining field experience with modern diagnostic tech, solar operators can maintain peak performance while ensuring system safety.