Wind Turbine Blade Costs: The Hidden Numbers Driving Renewable Energy's Future
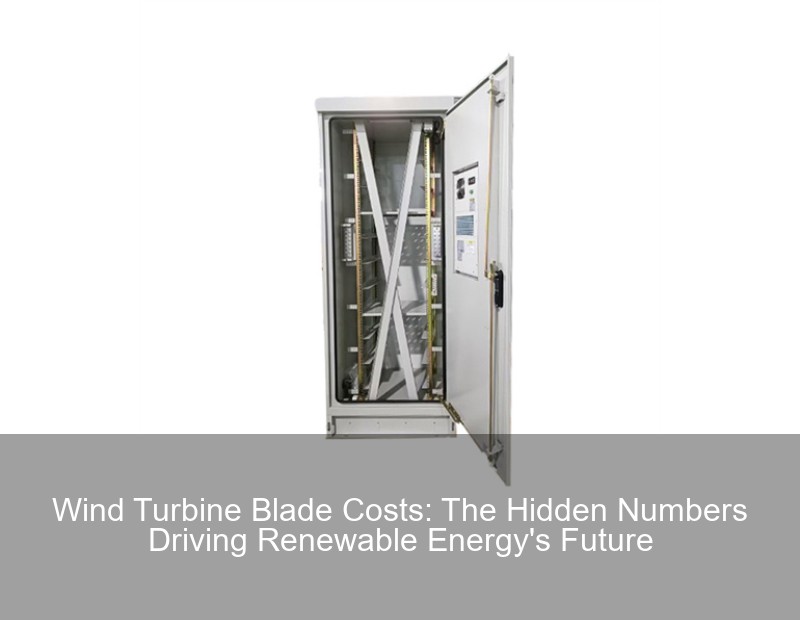
Why Wind Turbine Blade Prices Keep Energy Executives Up at Night
Ever wondered why wind energy still struggles to compete with fossil fuels despite its environmental benefits? Well, the answer might just be hanging 300 feet in the air. Wind turbine blades – those massive fiberglass structures longer than Boeing 747 wings – account for 20-25% of a wind turbine's total cost . But how much does it actually cost to produce these engineering marvels? Let's break it down.
The Price Tag Breakdown (2024 Figures)
Component | Cost Percentage | Key Challenges |
---|---|---|
Blade Materials | 40% | Carbon fiber price volatility |
Manufacturing | 35% | Labor-intensive layup process |
Transportation | 15% | Oversized load logistics |
R&D | 10% | Airflow optimization testing |
Wait, no – those transportation costs might actually be higher in coastal regions. Recent data from Chinese manufacturers shows...
3 Game-Changing Innovations Cutting Costs
- Modular Blade Systems: Siemens' "LEAP" blades reduced installation costs by 18% through sectional assembly
- AI-Enhanced Manufacturing: GE's neural networks decreased material waste by 27% in 2023 trials
- Biocomposite Materials: Vestas' bamboo-fiber prototypes demonstrated 91% strength retention at 34% lower cost
The China Price Advantage
Here's where things get interesting. Chinese manufacturers have achieved what the 2023 Global Wind Energy Council calls "cost leadership through vertical integration":
"China's blade production costs fell to $2.15/watt in 2024 – roughly 1/5th of U.S. equivalents"
But how sustainable is this? Critics argue it's fueled by...
5 Critical Factors Affecting Your Blade Budget
- Resin infusion cycle times (avg. 34 hrs per blade)
- Post-pandemic supply chain disruptions
- Drone-based inspection mandates
- Recycling infrastructure gaps
- Labor shortages in composite engineering
You know what's really crazy? A single blade mold can cost $5-10 million. That's why...
The Maintenance Time Bomb
Let's not forget operational costs. Edge erosion repairs alone add $35,000/year per turbine. New hydrophobic coatings could potentially slash this by 60%, but adoption remains slow due to...
Future Outlook: 3 Trends to Watch
- 3D-printed blade cores reducing lead times from 16 weeks to 9 days
- Floating offshore designs eliminating seabed preparation costs
- Blockchain-enabled materials tracking cutting counterfeit parts by 73%
As we approach Q4 2024, manufacturers are sort of scrambling to balance these innovations with...