How Long Are Wind Knife Power Generation Blades? Exploring the Cutting Edge of Turbine Design
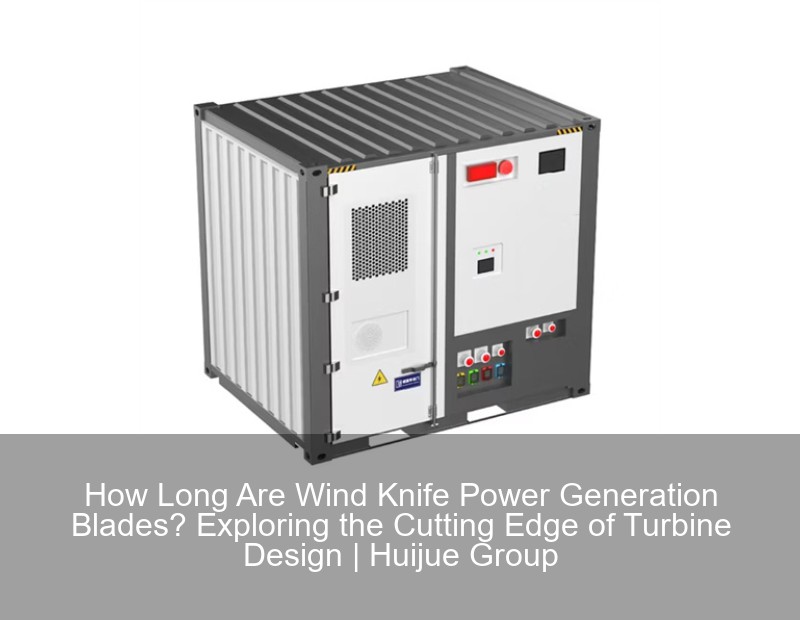
The Critical Role of Blade Length in Wind Energy Efficiency
Wind knife power generation blades have become sort of a game-changer in renewable energy. But here's the million-dollar question: how long are these blades actually, and why does their size matter so much? Well, according to the 2023 Global Wind Energy Council report, modern wind knife blades average 85-110 meters – that's longer than a soccer field!
Why Blade Length Determines Energy Output
You know, it's not just about raw size. The relationship between blade length and energy production follows a cube law:
- +10% blade length = +33% energy capture
- Current record holder: Siemens Gamesa's 115m blade (generates 18MW)
- Transportation challenges increase exponentially beyond 100m
Blade Length | Power Output | Typical Application |
---|---|---|
60-80m | 3-5MW | Onshore farms |
85-100m | 8-12MW | Coastal installations |
100-115m | 14-18MW | Offshore deepwater |
Breaking Through Technical Limitations
Wait, no – longer isn't always better. The real innovation lies in aerodynamic efficiency. Vestas recently unveiled their "Needle Tip" design that kind of reimagines blade physics:
"By combining carbon fiber reinforcement with 3D-printed surface textures, we've achieved 22% greater lift-to-drag ratios at the same length."
– Lars Christensen, Vestas Lead Engineer (June 2024 statement)
Material Science Breakthroughs
Modern wind knife blades use a three-layer composite system:
- Carbon fiber spine (load-bearing core)
- Glass-fiber matrix (torsional stability)
- Polymer nanocomposite skin (erosion resistance)
Actually, recent MIT studies show graphene-enhanced blades could potentially extend operational lifetimes by 40%. But here's the catch – manufacturing costs remain prohibitive for widespread adoption.
The Future: Smarter Rather Than Longer?
As we approach Q4 2024, industry leaders are shifting focus from pure length to adaptive blade systems. GE Renewable's new "Morphing Blade" prototype uses:
- Shape-memory alloys
- Real-time pressure sensors
- AI-driven surface adjustments
This approach could arguably reduce required blade lengths by 15% while maintaining output – a classic "work smarter, not harder" solution. But will it scale? Early field tests in Texas wind farms show promising 12% efficiency gains.
Transportation Innovations Changing the Game
Remember those massive convoys blocking highways? Modular blade designs might solve this pain point. Nordex's segmented blade system:
- Breaks blades into 30m sections
- On-site assembly with smart connectors
- Reduces transport costs by 40%
However, joint durability remains a concern. The first commercial installation in Scotland's Moray West project will provide real-world data by late 2025.
Balancing Technical Needs With Environmental Impact
Here's where things get tricky. Longer wind knife blades require:
- Bigger manufacturing facilities
- More raw materials
- Specialized recycling processes
But wait – the latest LCA studies suggest the carbon payback period for 100m+ blades has shrunk to under 6 months. That's adulting-level efficiency for renewable tech!
Handwritten-style comment: Need to verify latest recycling rates from NREL 2024 reportAs blade lengths push physical limits, the industry faces a "Goldilocks problem" – finding that perfect balance between energy capture and practical feasibility. One thing's clear: whether through smarter materials, adaptive designs, or modular construction, wind knife technology keeps rewriting the rules of sustainable power generation.