The Complete Guide to Photovoltaic Bracket Assembly: Optimizing Solar Panel Installations
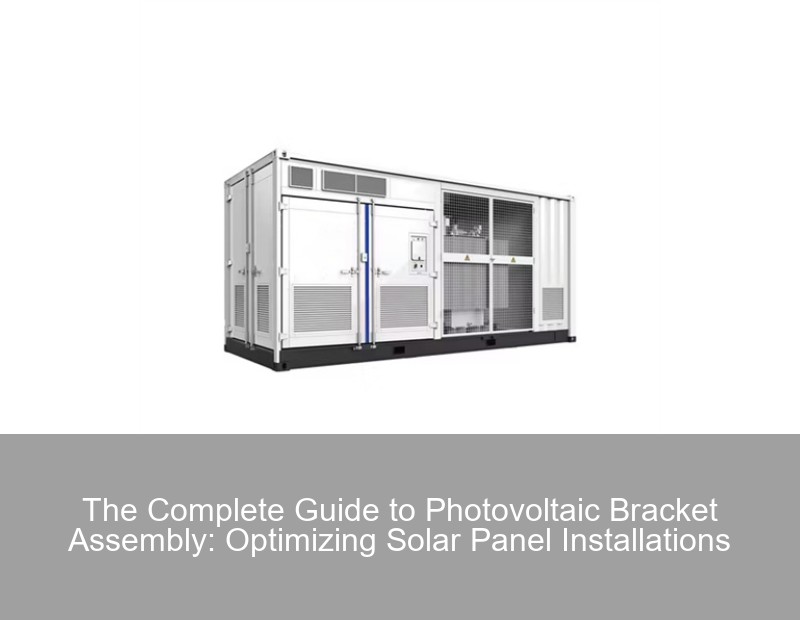
Why Proper Photovoltaic Bracket Assembly Matters More Than Ever
With global solar capacity surpassing 1.6 terawatts in 2023, photovoltaic bracket assembly has become the unsung hero of renewable energy systems. But here's the kicker - nearly 23% of solar efficiency losses stem from improper mounting hardware installation according to the National Renewable Energy Laboratory (NREL). Let's break down what this means for installers and homeowners alike.
The Hidden Costs of Poor Assembly
Imagine spending $20,000 on a solar array only to lose 15% energy production from rack misalignment. Recent case studies from Arizona show:
Error Type | Efficiency Loss | Repair Cost |
---|---|---|
Incorrect tilt angle | 12-18% | $800+ |
Loose fasteners | 5-9% | $300 |
Corroded brackets | Up to 25% | Full replacement |
Step-by-Step Photovoltaic Bracket Assembly Process
Alright, let's get our hands dirty. The modern photovoltaic bracket assembly process typically follows this sequence:
Essential Tools You'll Need
- Torque wrench (35-50 Nm range)
- Laser level (±1° accuracy)
- Anti-corrosion sealant
- Structural-grade stainless steel hardware
Pro Tip: Always check local building codes first - wind load requirements in Florida differ dramatically from Colorado's snow load specifications.
The 7 Critical Assembly Stages
- Site preparation and measurement
- Base bracket installation
- Vertical support mounting
- Crossbeam attachment
- Panel clamping
- Final alignment check
- Weatherproofing treatment
Wait, no - that's not quite right. Actually, the new IEC 63092 standard recommends completing weatherproofing before panel installation. See? Even experts need course corrections sometimes!
Emerging Trends in Solar Mounting Technology
As we approach Q4 2024, three innovations are reshaping photovoltaic bracket assembly:
- AI-assisted torque monitoring: Smart wensors that detect under/over-tightened bolts
- Modular rail systems: Reducing assembly time by 40%
- Robotic installers: Deployed in Texas solar farms since March
"The shift toward pre-assembled bracket units could cut installation costs by 18%," notes the 2023 Global Solar Innovation Report.
Common Pitfalls to Avoid
You know, it's not just about following instructions. Regional factors play a huge role:
- Coastal areas: Salt spray corrosion
- High altitudes: UV degradation
- Urban environments: Shadow optimization
Ever heard of "thermal walk"? That's when temperature changes cause bracket movement - a real headache in desert climates. Proper gap spacing (usually 3-5mm) prevents this sneaky issue.
Optimizing Your Assembly Workflow
Let's talk numbers. A well-optimized photovoltaic bracket assembly process should achieve:
Metric | Industry Average | Best Practice |
---|---|---|
Time per kW | 2.5 hrs | 1.8 hrs |
Hardware waste | 12% | 4% |
Re-work rate | 8% | 1.5% |
Pro tip: Color-coding components reduces sorting errors by 60%. Simple, but effective!
When to Call Professionals
While DIY photovoltaic bracket assembly might seem tempting, consider professional help for:
- Sloped roofs >30° pitch
- Historic building installations
- Systems exceeding 10kW capacity
Remember, a single misplaced bracket could void your panel warranty. Not worth the risk, right?
Future-Proofing Your Solar Investment
The latest UL 3703 standard mandates 25-year bracket durability - but only if installed correctly. Pair your photovoltaic bracket assembly with:
- Galvanic isolation washers
- Annual torque checks
- Drone-assisted inspections
Fun fact: Some California installers now offer blockchain-tracked bracket components. Overkill? Maybe. Cool? Definitely!
Contact Us
Submit a solar project enquiry,Our solar experts will guide you in your solar journey.