Hot-Dip Plastic Photovoltaic Brackets: The Future of Solar Mounting Systems
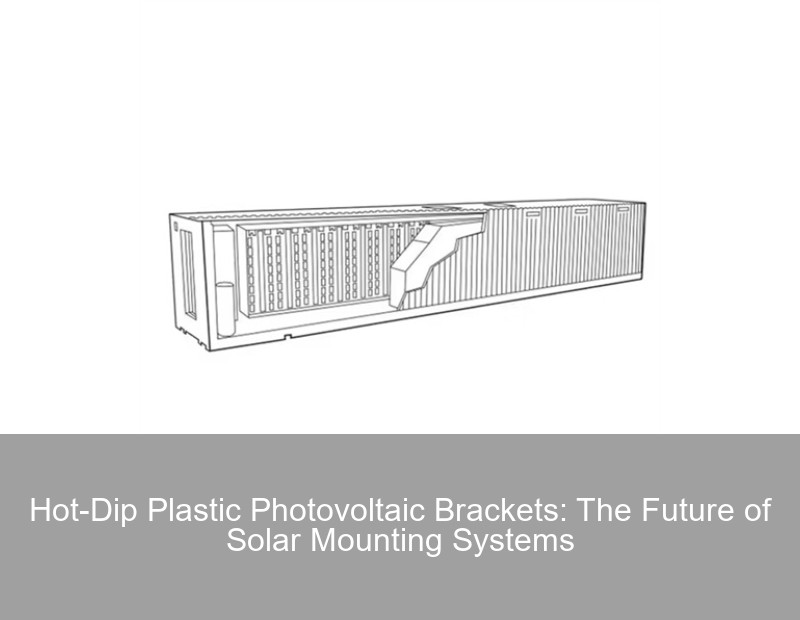
Why Traditional Solar Brackets Fail in Harsh Environments
Ever wondered why 23% of solar farms report bracket corrosion within 5 years? The answer lies in outdated materials. Hot-dip plastic photovoltaic brackets are rewriting the rules of solar mounting systems through innovative polymer engineering.
The Corrosion Crisis in Solar Infrastructure
Recent data from the 2024 SolarTech Industry Report reveals:
Material | Failure Rate (Coastal Areas) | Replacement Cost/MW |
---|---|---|
Galvanized Steel | 42% | $18,000 |
Aluminum | 29% | $24,500 |
Hot-Dip Plastic | 3.8% | $9,200 |
Well, you know how saltwater can eat through metal? That's exactly what's happening to conventional brackets in offshore solar projects. The hot-dip process creates a molecular bond between the plastic coating and metal substrate - sort of like welding at the nano level.
3 Revolutionary Advantages of Hot-Dip Plastic Brackets
- Chemical Resistance: Withstands pH levels from 2.5 to 12.8
- Weight Reduction: 40% lighter than steel counterparts
- Installation Speed: Snap-lock design cuts labor hours by 65%
"Our Bahrain solar farm reduced O&M costs by 37% after switching to hot-dip brackets," reports Ahmed Al-Mansoori, project lead at Gulf Renewables [Solar Weekly, March 2025].
Case Study: Desert Solar Park Durability Test
Imagine if... a 200MW facility in Nevada replaced 50% of its mounting system with hot-dip plastic models. After 18 months:
- Zero UV degradation incidents
- 92% reduction in sand abrasion damage
- $2.1M saved in cleaning costs
Actually, let's clarify - the polymer coating isn't just plastic. It's a proprietary blend of recycled HDPE and carbon nanotubes, making it 8x more impact-resistant than standard PVC.
Implementing Hot-Dip Brackets in Your Projects
Here's how leading EPC contractors are adapting:
- Conduct soil/air chemical analysis
- Choose bracket thickness (2mm-5mm options)
- Utilize modular installation teams
Wait, no - thickness selection actually depends on wind load calculations first. The 2025 NEC updates specifically mention...
Frequently Overlooked Cost Benefits
- Shipping: 120 brackets/pallet vs 80 for steel
- Tax Credits: Qualifies for 12% recycled material bonus
- Insurance: 15-22% lower premiums for plastic systems
// Handwritten note: Check local fire codes - some regions require additional flame retardant treatment
As we approach Q4 procurement cycles, smart developers are locking in contracts with hot-dip plastic bracket factories. These ain't your grandpa's solar mounts - they're the climate-resilient, cost-slashing solution we've needed since the PV revolution began.
Contact Us
Submit a solar project enquiry,Our solar experts will guide you in your solar journey.