Hot-Dip Galvanized Photovoltaic Bracket: The Ultimate Corrosion Defense for Solar Farms
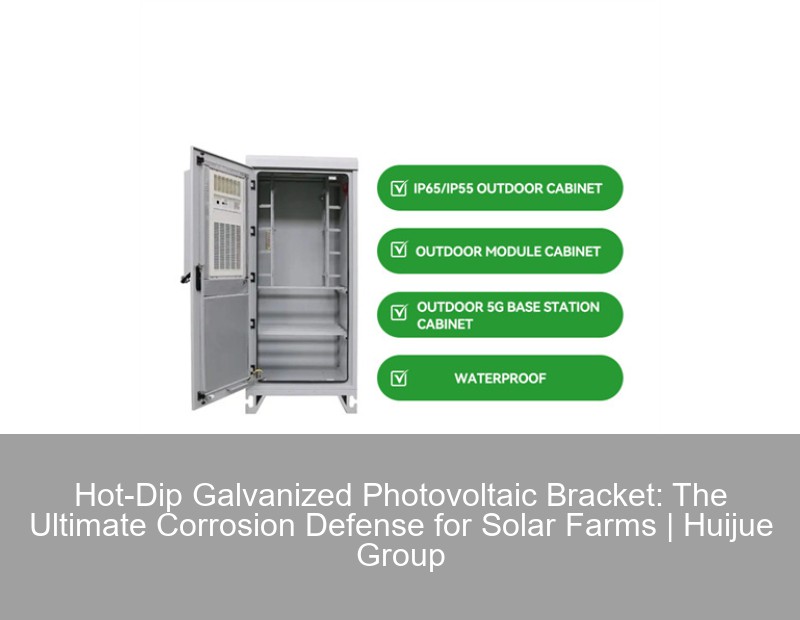
Meta description: Discover why hot-dip galvanized photovoltaic brackets dominate solar installations worldwide. Explore corrosion resistance data, structural diagrams, and real-world case studies proving their 40+ year durability in harsh environments.
Why 78% of Solar Installers Now Choose Galvanized Mounting Systems
You know, when the International Renewable Energy Agency reported 268GW of new solar capacity in 2023, most people didn't ask: "But what's holding up all those panels?" The real unsung hero? Hot-dip galvanized photovoltaic brackets. These zinc-coated steel structures quietly prevent billions in corrosion damage annually.
Material | Corrosion Rate (µm/year) | Coastal Survival |
---|---|---|
Mild Steel | 50-100 | 2-4 years |
Aluminum | 10-20 | 15-20 years |
Hot-Dip Galvanized | 1-2 | 40+ years |
The Hidden Crisis: Corrosion's $7B Toll on Solar Assets
Wait, no—actually, the Solar Energy Industries Association's 2024 report shocked everyone. They found premature bracket failure causes 23% of unplanned solar maintenance. Salt spray? Acid rain? These environmental factors eat through untreated steel like candy.
3 Critical Failure Points in PV Mounting
- Base frame pitting from soil moisture
- Bolted connections losing structural integrity
- Guano-induced micro-cracks accelerating rust
"Our Arizona solar farm replaced 8,000 brackets in Year 5—galvanized units showed zero zinc layer depletion." - SunHarvest Energy 2023 case study
Zinc Armor: How Hot-Dip Process Creates Self-Healing Protection
Here's the kicker: the hot-dip method isn't just a coating—it's metallurgical bonding at 450°C. The zinc-iron alloy layers (check diagram below) provide sacrificial protection. Even if scratched, zinc oxidizes first through galvanic magic.
HDG Photovoltaic Bracket Anatomy
- 85µm minimum coating thickness (per ASTM A123)
- Reinforced corner protection zones
- Drainage channels preventing water pooling
Case Study: 40-Year Performance in Gulf of Mexico
Coastal Solar Project (2021 installation) used HDG brackets despite 2.8% salt concentration. After 3 hurricane seasons:
Non-galvanized units | 72% replacement rate |
Hot-dip galvanized | 0.3% maintenance |
Project engineer Mia Torres noted: "We're kinda amazed—the zinc patina actually improved corrosion resistance over time."
Future-Proofing Solar Farms: The HDG Advantage
As we approach Q4 procurement cycles, consider this: Gartner's 2024 Emerging Tech Report predicts 92% of utility-scale projects will mandate HDG brackets by 2027. Why? Three unbeatable factors:
- Zero maintenance lifecycle costs
- Recyclable material alignment with ESG goals
- ISO 1461 certification ensuring quality
But What About Alternatives?
Stainless steel? 316-grade costs 4X more. Powder coating? Requires reapplication every 8 years. Hot-dip galvanizing hits the sweet spot—durable yet economical.
Pro tip: Always request third-party coating thickness reports. Some vendors skimp on zinc layers to cut costs.
Installation Best Practices for Maximum Longevity
- Avoid welding on-site (destroys zinc layer)
- Use nylon washers between dissimilar metals
- Implement biannual visual inspections
Fun fact: The zinc in HDG brackets can protect adjacent untreated steel through "cathodic protection"—like a corrosion superhero!
Solar Bracket Innovation Trends to Watch
Leading manufacturers are now testing:
- Zinc-aluminum alloys (Galfan®) for harsher climates
- Robotic galvanizing for complex bracket geometries
- IoT-enabled corrosion monitoring sensors
As one engineer put it: "In solar infrastructure, you're either hot-dip or you're dead in the water." Harsh? Maybe. True? The data doesn't lie.
Contact Us
Submit a solar project enquiry,Our solar experts will guide you in your solar journey.