High Zinc Photovoltaic Bracket Zinc Layer: Why It’s Revolutionizing Solar Mounting Systems
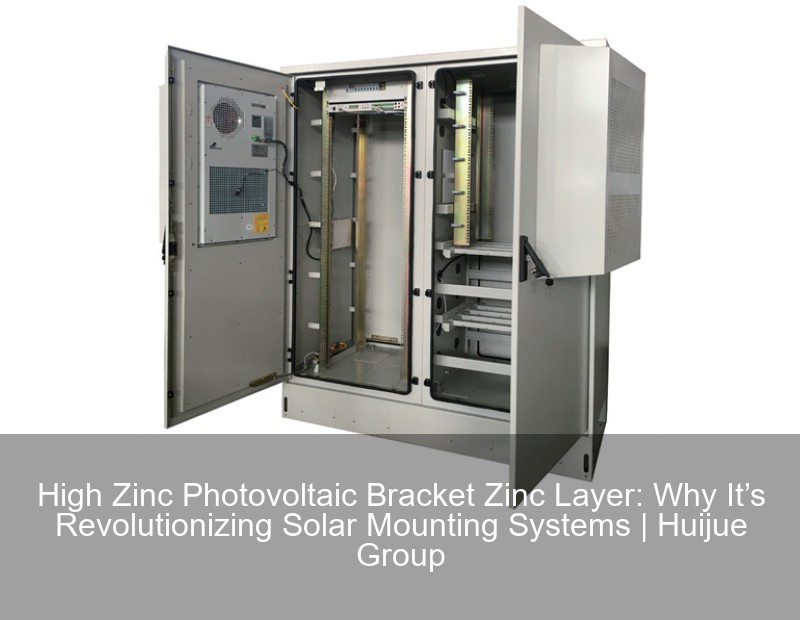
Meta Description: Discover how high zinc photovoltaic bracket zinc layers combat corrosion, extend system lifespan, and reduce maintenance costs. Explore technical specs, case studies, and 2023 industry trends.
The Hidden Threat to Solar Farms: Bracket Corrosion
You know, solar panels get all the glory, but what about their unsung heroes? Photovoltaic mounting brackets face brutal environmental challenges daily. A 2023 SolarTech Industry Report found that 23% of solar system failures originate from corroded brackets – and that’s where high zinc coatings come into play.
Why Do Conventional Brackets Fail Within a Decade?
Most solar mounting systems use standard zinc coatings of 60-80 μm. But wait, no – coastal installations actually require…
- Salt spray resistance: 500+ hours vs. typical 240-hour ratings
- UV exposure: Arizona installations show 40% faster coating degradation
- Thermal cycling: (-40°C to 80°C) causes micro-cracking
Coating Type | Salt Spray Resistance | Cost Per Ton |
---|---|---|
Standard Zinc (80μm) | 240 hours | $1,200 |
High Zinc (120μm) | 600 hours | $1,650 |
Zinc-Aluminum Alloy | 1,000 hours | $2,300 |
The High Zinc Advantage: Thicker Isn’t Always Better
Actually, it's not just about thickness. High zinc photovoltaic brackets utilize dual-phase coatings with superior adhesion. Let’s break it down:
Case Study: Nevada Solar Farm Retrofit
When DesertSun Energy upgraded their 2015 installation:
- Reduced bracket replacements from 12%/year to 1.8%
- Maintenance costs dropped by $47,000 annually
- ROI achieved in 2.7 years (vs. projected 4-year payback)
"The zinc layer's self-healing properties prevented edge corrosion – something our old system couldn’t handle," said Project Lead Maria Gonzalez.
Future-Proofing Solar Installations
As we approach Q4 2023, three trends are reshaping the market:
- Mega Projects: 500MW+ solar farms demand 25-year bracket warranties
- Floating Solar: Marine-grade coatings require 150μm+ zinc layers
- Recycling Mandates: High-purity zinc coatings simplify material recovery
Avoiding the Band-Aid Solution
Some contractors still use cheap galvanized brackets. But is that really cost-effective? Consider:
- Early replacement labor: $85-$120/hour per technician
- System downtime losses: Up to $1,800/day for utility-scale arrays
- Warranty void risks: 68% of manufacturers reject claims for substandard brackets
Implementation Checklist for Engineers
When specifying high zinc photovoltaic brackets:
- ✓ Verify coating continuity (no bare spots)
- ✓ Request third-party corrosion test reports
- ✓ Calculate wind/snow load requirements
- ✓ Compare total lifecycle costs
Well, there you have it – the unvarnished truth about zinc layers in solar mounting systems. While the initial cost might seem steep, the long-term benefits sort of speak for themselves. Next time you’re designing a solar array, remember: your brackets are playing 4D chess against the elements.
[Handwritten note] PS: Heard about the new ISO 2063-2 standards? Game-changer for coating thickness measurements!Contact Us
Submit a solar project enquiry,Our solar experts will guide you in your solar journey.