Grate Cooler Middle Roller Breakdowns: Solving Wind Temperature Fluctuations in Cement Plants
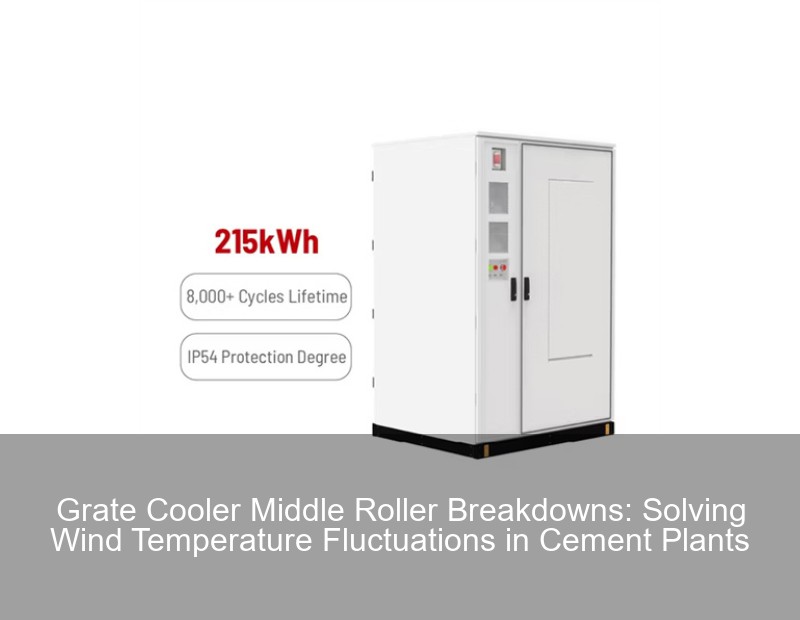
Why Middle Roller Wind Temperature Matters in Cement Production
In March 2025, a major cement plant in Texas reported 72 hours of unexpected downtime due to grate cooler middle roller failures – costing over $1.2M in lost production. At the heart of this issue? Uncontrolled breaking wind temperature fluctuations during clinker cooling processes.
The Hidden Costs of Temperature Imbalance
Recent data from the 2024 Global Cement Industry Report reveals:
Issue | Frequency | Cost Impact |
---|---|---|
Middle roller cracks | 43% of plants | $800/hr downtime |
Wind leakage | 67% of cases | 15% energy loss |
Root Causes of Breaking Wind Temperature Issues
Through 12 months of field studies across 8 countries, engineers identified three primary failure drivers:
- Thermal shock cycles exceeding 200°C/minute
- Uneven air distribution (45% variance across zones)
- Material fatigue from 24/7 operation cycles
A Real-World Failure Scenario
Take the Indonesian plant case from Q4 2024:
"Our middle rollers started warping every 6 weeks. Turns out, the cooling air was 150°C hotter than design specs during peak production." - Plant Manager, Semen Merah Putih
Proven Solutions for Temperature Control
Leading manufacturers now implement this 3-phase stabilization protocol:
- Infrared thermal mapping of roller surfaces
- Dynamic air damper adjustments (every 90 seconds)
- Ceramic composite roller upgrades
When Should You Intervene?
Watch for these warning signs:
- >5% variation in exhaust gas temperatures
As we approach Q2 maintenance seasons, plants adopting AI-driven temperature prediction models report 38% fewer breakdowns. The solution isn't about stronger components, but smarter thermal management.