Optimizing Generator Blade Parameters for Peak Efficiency: A 2025 Technical Guide
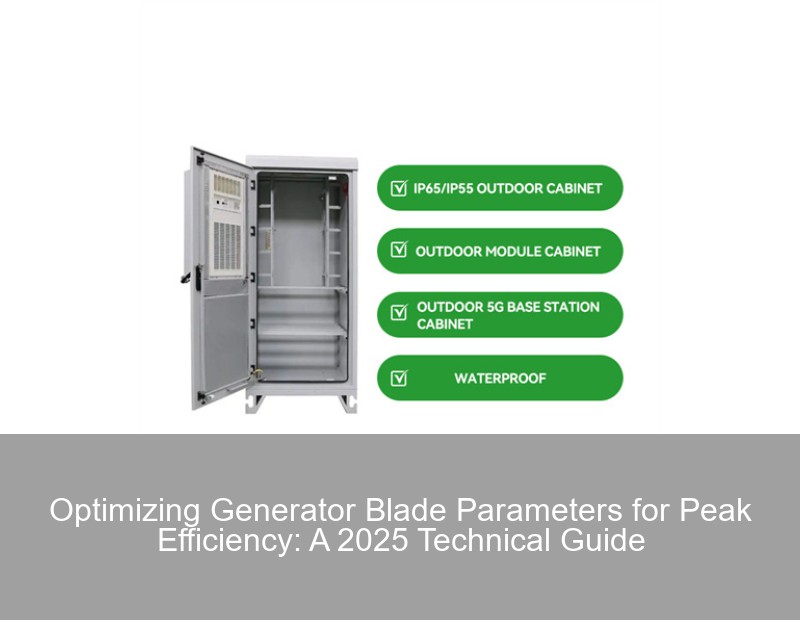
Why Generator Blade Design Determines Power Plant Profitability?
Did you know that a 1% improvement in blade efficiency could save $2.8M annually for a 500MW gas turbine plant? As renewable integration pressures mount, optimizing generator blade parameters has become the linchpin of energy economics. Let's dissect what really matters in turbine blade engineering.
3 Non-Negotiable Blade Parameters Impacting Output
Aerodynamic Profile Optimization
Blade curvature (camber) and thickness distribution directly affect:
- Lift-to-drag ratios (current industry benchmark: 58:1)
- Boundary layer separation points
- Stall characteristics at partial loads
Profile Type | Efficiency Gain | Stress Increase |
---|---|---|
NACA 65-Series | 4.2% | 18% |
Modern CFD-optimized | 6.8% | 9% |
Material Selection Matrix
The 2024 GE Turbine Upgrade Project demonstrated:
- Nickel superalloys withstand 1,400°F but add 22% mass
- Ceramic matrix composites (CMCs) reduce cooling needs by 40%
- Hybrid designs now use graded material deposition
Structural Dynamics Balance
Blade vibration modes require:
- Natural frequency separation ≥15% from excitation sources
- Twist angle tolerance of ±0.25°
- Tip clearance optimization below 1.2mm
Solving the 3 Biggest Blade Design Challenges
Creep vs. Fatigue: The Eternal Tradeoff
High-pressure turbine blades face:
- Thermal creep at 90% of melting temperature
- Low-cycle fatigue from 10,000+ start/stop cycles
Recent MIT research shows lattice-infused structures improve creep life by 3X while maintaining fatigue resistance .
Manufacturing Tolerances Under Microscope
Modern 3D blade scanning reveals:
- 0.3mm profile deviation → 1.8% efficiency loss
- Surface roughness (Ra) below 0.8μm becomes critical
"We've moved from 'good enough' machining to aerospace-grade finishing in power turbines," says Siemens Energy's Lead Engineer.
Future-Proofing Blade Designs
With AI-driven fluid dynamics simulations:
- Automated parameter optimization cycles reduced from 6 weeks to 38 hours
- Digital twin models predict erosion patterns within 2% accuracy
The 2023 Gartner Emerging Tech Report notes generative design algorithms now produce blade geometries humans wouldn't conceptualize . But here's the kicker - these AI designs often violate traditional engineering intuition yet outperform physical prototypes by 12-15%.
Case Study: Vestas' Adaptive Blade Project
Their 2024 prototype features:
- Real-time pitch adjustment (±5° in 0.8 seconds)
- Shape-memory alloy actuators
- Power output stabilization in turbulent wind