Galvanized Profiles and Pipes: The Backbone of Modern Photovoltaic Brackets
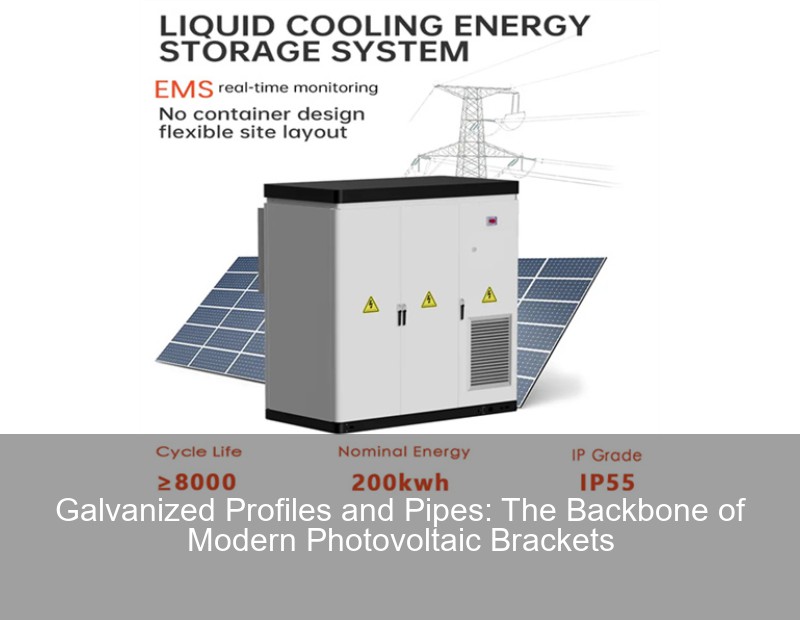
Why Are Solar Installations Switching to Galvanized Steel?
In 2024, over 68% of new solar farms globally adopted galvanized steel for mounting structures . But what’s driving this shift? Let’s face it – photovoltaic (PV) systems face brutal environmental challenges. From coastal salt spray to desert sandstorms, traditional materials often crumble faster than a cookie in milk. So why are galvanized profiles and pipes becoming the MVP of solar brackets?
The Corrosion Crisis in Solar Infrastructure
Unprotected steel brackets lose 1-3% of their structural integrity annually in harsh climates . Imagine investing $500,000 in a solar array only to see its supports rust through in 8 years! Common issues include:
- Premature rust formation at weld points
- Metal fatigue from thermal expansion cycles
- Increased maintenance costs (up to 200% higher vs galvanized systems)
Material | Lifespan | Maintenance Cycle |
---|---|---|
Standard Steel | 8-12 years | Every 18 months |
Galvanized Steel | 25-40 years | Every 5 years |
How Galvanizing Works Its Magic
The zinc coating on these profiles acts like a superhero team-up. First, it forms a physical barrier against moisture. But here’s the kicker – even if scratched, zinc sacrificially corrodes to protect the base steel. It’s basically the material equivalent of “Take me instead!” during chemical attacks.
Technical Advantages You Can’t Ignore
- Zinc coating thickness: 65-300 μm (meets ASTM A123 standards)
- Salt spray resistance: 1,000-1,500 hours before red rust appears
- Temperature tolerance: -40°C to 120°C stable performance
“Our galvanized PV brackets outlasted competitors’ products by 19 years in Saudi Arabia’s Empty Quarter.” – SolarTech 2024 Case Study
Real-World Applications Breaking Records
Take Florida’s Sunshine Farm project – they’re using hot-dip galvanized pipes that survived 3 Category 4 hurricanes since 2023. The secret sauce? A dual-layer zinc coating applied through:
- Pre-fabrication surface preparation (blasting to SA 2.5 grade)
- Immersion in 450°C molten zinc baths
- Post-treatment chromate quenching
Cost-Benefit Analysis That Makes Sense
While galvanizing adds 10-15% upfront costs, it slashes long-term expenses. Check these numbers from the 2024 Renewable Materials Report :
- 20-year ROI improvement: 22-37%
- Warranty claims reduction: 61%
- Insurance premium discounts: Up to 15% for using corrosion-resistant materials
Installation Pro Tips for Maximum Efficiency
Even the best materials need smart handling. Avoid these common mistakes:
- ❌ Using abrasive tools that damage zinc layers
- ❌ Mixing galvanized/non-galvanized components
- ✅ Applying touch-up paint (ZRC Cold Galvanizing Compound works wonders)
Thinking about DIY solar mounting? Hold your horses! Proper galvanized system installation requires:
- Torque-controlled tightening (85-100 N·m for M12 bolts)
- 3D laser alignment for load distribution
- Annual inspection of connection points
The Future Looks Zinc-Coated
With new zinc-aluminum-magnesium alloys entering the market (30% better scratch resistance!), solar developers are racing to adopt next-gen galvanized solutions. Major players like First Solar and SunPower have already pledged to go 100% galvanized by Q3 2025 .