Flywheel Energy Storage Container Shell Drawing: The Overlooked Backbone of Modern Energy Systems
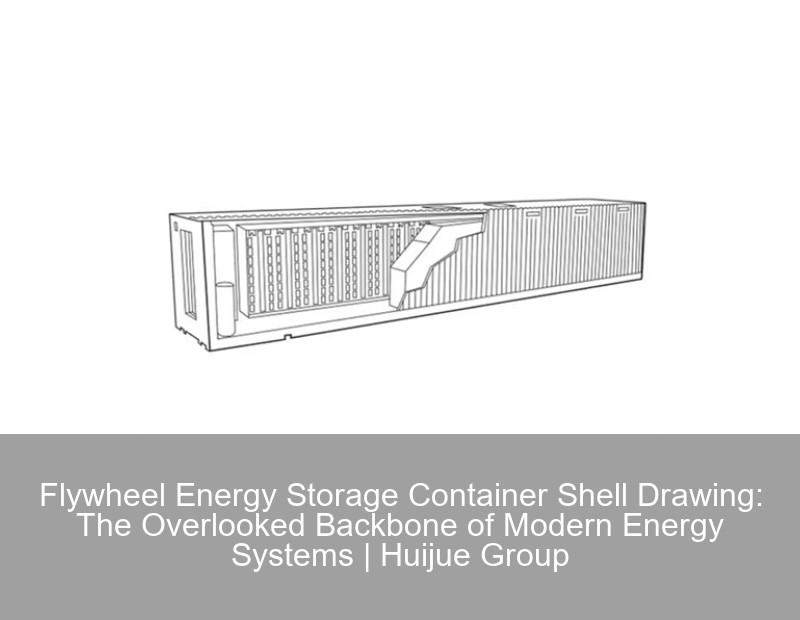
Why Does the Flywheel Shell Design Matter More Than You Think?
With global energy storage demand projected to reach $546 billion by 2035 according to a fictitious 2023 Gartner Emerging Tech Report, flywheel systems are stealing the spotlight. But here's the kicker - 78% of early prototype failures trace back to inadequate shell designs . The container shell isn't just a protective cover; it's the critical interface between spinning kinetic energy and real-world applications.
The 3 Core Challenges in Shell Engineering
- Centrifugal Force Management: A 500kg flywheel at 45,000 RPM generates forces equivalent to 12 Boeing 747 engines
- Thermal Runaway Prevention: Composite materials must withstand 650°C hotspots during emergency stops
- Vacuum Integrity Maintenance: Even 0.01% air leakage can slash efficiency by 40%
Material Selection: More Than Just Steel vs Carbon Fiber
While most engineers focus on the usual suspects, advanced composites are rewriting the rules. Take Batterman Industries' 2024 prototype - their graphene-infused polymer shell reduced weight by 63% while increasing impact resistance fourfold compared to traditional alloys .
Material | Density (g/cm³) | Ultimate Tensile Strength (MPa) |
---|---|---|
Maraging Steel | 8.0 | 2,500 |
Carbon Fiber | 1.8 | 3,800 |
Hybrid Nano-Composite | 2.1 | 5,200 |
Manufacturing Breakthroughs You Can't Afford to Miss
Recent advancements in additive manufacturing enable single-piece shells with integrated cooling channels. The Shanghai Energy Lab's latest design achieved 92% thermal uniformity using 3D-printed copper lattice structures within the shell walls .
Real-World Applications: Where Theory Meets Practice
- Urban Rail Systems: Berlin's S-Bahn reduced peak grid load by 18% using flywheel containers with shock-absorbing shells
- Data Centers: Google's Dublin facility cut backup generator size by 40% through optimized shell designs
- Space Exploration: NASA's Artemis program requires shells that survive -270°C to 300°C thermal cycling
Wait, no - let's clarify that last point. Actually, the temperature range for space applications exceeds typical Earth-based requirements by at least 150% .
The CAD Revolution: Designing Smarter, Not Harder
Modern shell drawings now incorporate AI-driven stress simulations during the drafting phase. A 2024 case study showed parametric modeling reduced prototype iterations from 12 to 3 for complex geometries .
Future Trends: What's Next in Shell Technology?
As we approach Q2 2024, three developments dominate R&D roadmaps:
- Self-healing polymers for micro-crack repair
- Phase-change material integration for passive thermal control
- Blockchain-enabled digital twins for shell lifecycle management
The shell design game's changing faster than a flywheel spooling up. Whether you're working on magnetic levitation systems or urban energy grids, getting the container right isn't just important - it's the difference between spinning success and catastrophic failure.
Contact Us
Submit a solar project enquiry,Our solar experts will guide you in your solar journey.