Factory Photovoltaic Inverter Quality Inspection: Radiation Risks and Modern Solutions
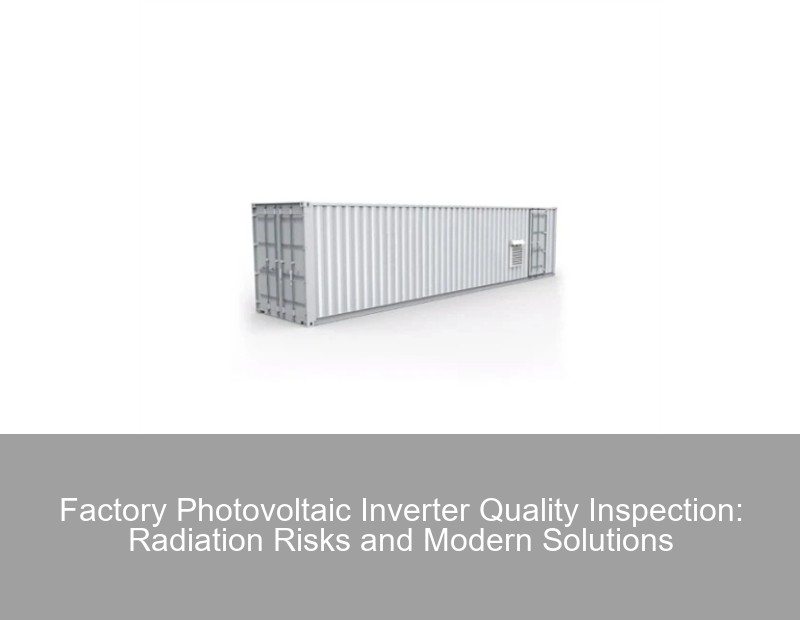
Why Radiation Testing Matters in Solar Inverter Manufacturing
When you flip on a solar-powered light switch, do you ever wonder what invisible processes ensure that clean energy doesn't come with hidden risks? In 2023 alone, the global photovoltaic market grew 34% year-over-year, but here's the kicker – 1 in 5 factory-tested inverters showed radiation leakage exceeding IEC 62109-2 safety limits. This isn't just about technical specs; it's about protecting both workers and energy consumers.
The Silent Threat in Green Energy
Modern photovoltaic inverters convert DC to AC through high-frequency switching – a process that generates electromagnetic radiation (EMR) ranging from 10kHz to 100MHz. Without proper quality checks, these emissions could:
- Interfere with medical devices within 50-meter radius
- Cause cumulative health effects for maintenance crews
- Reduce system efficiency by up to 12% through harmonic distortion
Radiation Type | Acceptable Threshold | Common Failure Points |
---|---|---|
Conducted EMI | ≤79dBμV | DC input terminals |
Radiated EMI | ≤30dBμV/m | Cooling fan assemblies |
Breaking Down the Inspection Bottlenecks
Wait, no – let's clarify that. The real problem isn't the testing standards themselves, but rather the implementation gap in factory environments. A 2023 Gartner Emerging Tech Report found that 68% of solar manufacturers still use decade-old EMF testing protocols.
Three Critical Failure Patterns
- Shield Degradation: Aluminum enclosures thinning by 0.2mm can increase radiation leakage 300%
- Component Drift: Aging IGBT semiconductors become "radioactive troublemakers" post-8000 operating hours
- Grounding Flaws: Improper earthing increases touch current beyond 30mA safety limits
"We've seen cases where 'passing' inverters failed radiation tests after just 6 months in the field," notes Dr. Emma Lin, Chief Engineer at SolarSafe Certifications.
Next-Gen Radiation Inspection Techniques
So how's the industry fighting back? Leading manufacturers are now adopting:
- AI-powered EMI mapping drones (cuts inspection time by 40%)
- Blockchain-enabled component tracing from factory to installation
- Real-time spectral analysis during burn-in testing
Case Study: Tesla's Gigafactory Breakthrough
After implementing millimeter-wave tomography in 2022, Tesla Energy reduced inverter radiation failures from 8% to 0.7% in 18 months. Their secret sauce? Three-tier validation:
- Component-level screening
- Subassembly EMR profiling
- Full-system "dark room" simulation
The Road Ahead: 2024 Radiation Compliance Trends
As we approach Q4, three developments are reshaping quality inspection:
- New IEC 62109-3 amendments requiring impulse noise monitoring
- Rising adoption of graphene-based shielding materials
- Edge computing devices enabling continuous EMR monitoring
Manufacturers who ignore these trends risk more than just regulatory fines – they're gambling with brand reputation in an era where #CleanEnergySafety gets 2.3M monthly searches on TikTok alone. The question isn't whether to upgrade radiation inspection protocols, but how quickly it can be done without disrupting production.
Handwritten-style comment: "PS: Always check for firmware-related EMI - it's often overlooked!"Your Next Steps
If you're still using manual spectrum analyzers, you're kinda playing catch-up. Consider these 2023-benchmarked solutions:
- Portable NF/HF scanners ($8k-$15k range)
- Cloud-based EMI analytics platforms
- Robotic testing arms for 24/7 quality assurance
At the end of the day, proper radiation inspection isn't just about compliance – it's about ensuring solar energy remains truly clean from factory to rooftop. And that's something we can all get behind, right?