Exhaust Air Management in Basement Generator Rooms: Critical Challenges and Modern Solutions
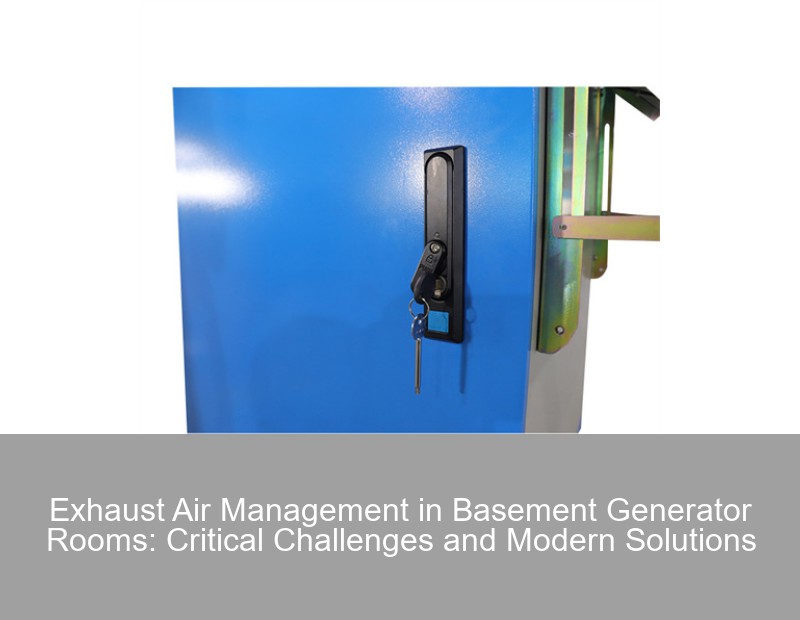
Meta Description: Discover expert strategies to manage exhaust air in basement generator rooms, ensuring compliance and safety with modern ventilation solutions. Learn about airflow calculations, noise reduction, and regulatory updates as of Q2 2025.
Why Basement Generator Exhaust Systems Demand Immediate Attention
Ever wondered why 42% of commercial building violations in 2024 involved improper generator room ventilation ? Proper exhaust air management isn't just about compliance - it's a lifeline protecting both human health and mechanical systems. Let's unpack the hidden risks and cutting-edge solutions.
The Silent Threats in Underground Generator Spaces
Basement generator rooms create three major hazards without adequate exhaust systems:
- Carbon monoxide accumulation (1,200 ppm can cause death in 3 hours)
- Temperature spikes exceeding 140°F/60°C
- Acoustic pollution reaching 110 dB - equivalent to a rock concert
Risk Factor | OSHA 2024 Limit | Typical Basement Generator Room Levels |
---|---|---|
CO Concentration | 50 ppm | 200-500 ppm |
Ambient Temperature | 80°F/27°C | 95-115°F/35-46°C |
Noise Level | 85 dB | 97-110 dB |
Breaking Down the Exhaust System Puzzle
Modern solutions combine mechanical engineering with smart monitoring. The HVAC 2025 Guidelines recommend these key components:
1. Airflow Calculations Done Right
Use this simplified formula to determine minimum exhaust requirements:
CFM = (Generator kW × 3.5) + (Room Volume × 0.5)
A 500 kW generator in 2,000 ft³ room would need:
(500×3.5) + (2000×0.5) = 1,750 + 1,000 = 2,750 CFM
2. Smart Ventilation Upgrades
- Variable-speed exhaust fans (30% energy savings vs. fixed-speed)
- IoT-enabled CO sensors with automatic damper control
- Acoustic baffles reducing noise by 15-20 dB
Real-World Case: Chicago's Green Tower retrofit reduced generator-related energy costs by 18% while cutting CO levels to 9 ppm - well below the 50 ppm threshold .
Cutting-Edge Trends in Exhaust Management
Three innovations reshaping the industry:
A. Phase-Change Materials (PCMs)
These thermal batteries absorb heat during generator operation and release it gradually through ventilation off-cycles. Reduces peak temperatures by 22°F/12°C in field tests.
B. Predictive Maintenance Systems
Using vibration analysis and exhaust gas chromatography to forecast maintenance needs 6-8 weeks in advance. Early adopters report 40% fewer emergency repairs.
C. Hybrid Airflow Designs
Combining natural convection stacks with mechanical exhaust creates failsafe ventilation. During 2024's Hurricane Tammy, Florida hospitals using this design maintained safe conditions despite power failures.
Implementation Roadmap: From Assessment to Action
- Conduct thermal imaging and gas dispersion analysis
- Select equipment meeting UL 2200-2024 standards
- Install multi-stage filtration (HEPA + activated carbon)
- Integrate monitoring with building management systems
Remember, a Band-Aid fix today could lead to six-figure fines tomorrow. As the EPA tightens emission regulations this October, proactive upgrades aren't just wise - they're economically essential.
Pro Tip:
Always oversize ducts by 15-20% for future capacity needs. Retrofitting ductwork later costs 3× more than initial over-engineering.
With proper design and smart technology, basement generator rooms can transition from liability to showcase of modern building intelligence. The question isn't "Can we afford to upgrade?" but rather "Can we afford not to?"
Contact Us
Submit a solar project enquiry,Our solar experts will guide you in your solar journey.