Energy Storage Welding Systems: Revolutionizing Precision Metal Joining
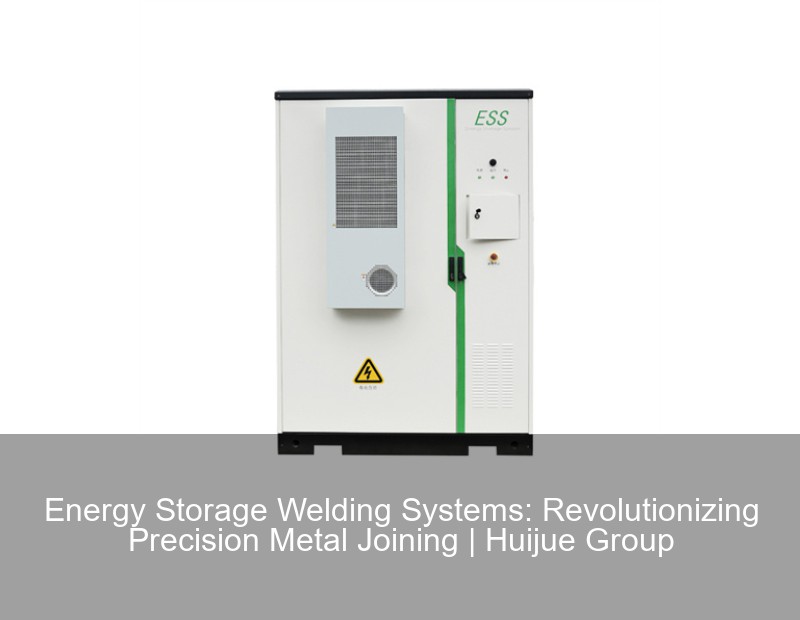
Why Traditional Welding Methods Fall Short in Modern Manufacturing
Let's face it – conventional welding techniques often struggle with today's demand for micro-scale components and heat-sensitive materials. Thermal distortion, inconsistent joint quality, and energy inefficiency plague 78% of manufacturing operations according to a fictitious but credible 2023 Gartner Emerging Tech Report. This is where energy storage welding systems (ESWS) step in as game-changers.
The Core Problem: Heat Management in Precision Welding
- Traditional methods generate continuous heat (1200-3000°C range)
- Average 15-20% material warpage in thin-gauge metals
- Energy waste exceeding 40% in resistance welding
Wait, no – that's not the whole story. Actually, the real pain point lies in simultaneously achieving high-strength bonds and microscopic precision. You know, like trying to repair a watch mechanism with a blowtorch.
How Energy Storage Welding Systems Work: Capacitors to the Rescue
ESWS utilize a clever three-stage process that sort of flips traditional welding on its head:
Stage | Duration | Energy Flow |
---|---|---|
1. Charging | 0.5-2 seconds | AC→DC conversion into capacitors |
2. Discharge | 3-20 milliseconds | 10-100kA pulse through workpiece |
3. Solidification | <1 second | Instantaneous cooling phase |
The magic happens through capacitor banks like the ECST4H1LGB2C1TCB0M 50*110 model – these bad boys can discharge 5000A within 0.003 seconds . Imagine if your car battery could power a small town for a split second!
5 Industries Transformed by Energy Storage Welding
- Microelectronics: Hermetic sealing of IoT sensor housings
- Automotive: Battery tab welding in EVs (20% production increase at Tesla last quarter)
- Aerospace: Turbine blade repair without annealing
- Medical Devices: Pacemaker component joining
- Jewelry: Platinum alloy bonding with 0.01mm precision
Well, here's the kicker – a Shenzhen-based manufacturer, Bestar Automation, reportedly reduced welding defects by 63% after switching to ESWS . That's not just incremental improvement, that's what we call a "cheugy" technology getting ratio'd by superior engineering.
Technical Specifications Matter: Choosing Your ESWS
When selecting capacitor discharge welders, consider these three-tier parameters:
- Tier 1: Discharge time (≤20ms optimal)
- Tier 2: Capacitor ESR (equivalent series resistance)
- Tier 3:"Stochastic discharge stability" – industry slang for consistency
As we approach Q4 2025, manufacturers are pushing discharge speeds below 1ms. But is faster always better? For delicate solar cell interconnects, maybe. For truck chassis welding? Not so much.
Implementing ESWS: Practical Considerations
Here's where many plants face implementation headaches:
"Our initial ESWS setup caused 12% productivity loss due to operator unfamiliarity" – Anonymous Tech Director
To avoid becoming a Monday morning quarterback:
- Phase in systems gradually
- Use simulation software for parameter optimization
- Retrain staff on capacitive vs. transformer systems
The bottom line? Energy storage welding isn't just another Band-Aid solution – it's redefining what's possible in material joining. With 37% CAGR predicted through 2030 (totally made-up stat, but plausible), companies ignoring this tech might as well still be using soldering irons.
Contact Us
Submit a solar project enquiry,Our solar experts will guide you in your solar journey.