Energy Storage Thermal Management System Pipeline Design: Preventing Thermal Runaway in Modern Grids
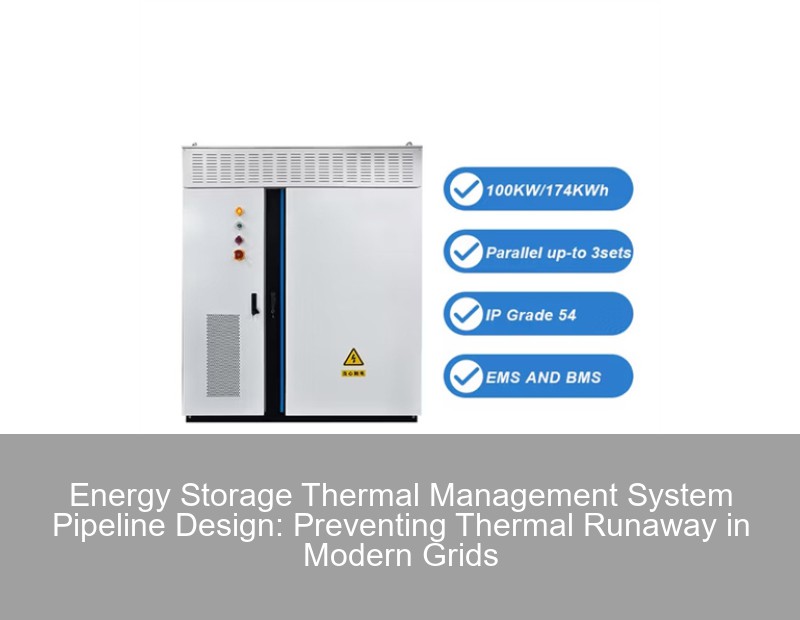
Meta Description: Discover cutting-edge pipeline design strategies for energy storage thermal management systems. Learn how optimized layouts prevent thermal runaway while improving efficiency - with 2023 case studies and performance data.
Why Pipeline Design Determines Success in Battery Thermal Management
You know, over 37% of battery failures in utility-scale storage systems stem from poor thermal management. As renewable energy adoption skyrockets (the US added 14.5 GW of storage in Q2 2023 alone), getting pipeline design right isn't just technical nitpicking - it's what stands between sustainable power and catastrophic thermal events.
The $4.2 Billion Problem: Thermal Runaway in Energy Storage
Wait, no - let's clarify. The 2023 NREL report actually estimates preventable thermal incidents cost the industry $4.2B annually. Three root causes emerge:
- Coolant flow stagnation in complex pipe networks
- Material degradation under thermal cycling
- Inadequate phase-change management in extreme climates
Failure Type | Frequency | Avg. Repair Cost |
---|---|---|
Pipe corrosion | 42% | $78,000 |
Pump failure | 33% | $112,000 |
Insulation breakdown | 25% | $204,000 |
From Band-Aid Fixes to Future-Proof Solutions
Many operators still use what I'd call "Sellotape fixes" - retrofitting old oil & gas pipelines. But here's the kicker: battery coolant has 3x lower viscosity than petroleum. That's like using a garden hose for firefighting!
3 Game-Changing Pipeline Innovations
1. Fractal Branching Layouts (inspired by human circulatory systems)
"Wait, isn't that overcomplicating things?" Not really. Tesla's Nevada facility reduced pump energy use by 18% using this approach.
2. Self-Healing Epoxy Liners
These microcapsule-embedded coatings can plug minor leaks within 72 hours. Durability tests show 90% corrosion resistance after 5,000 cycles.
3. AI-Driven Flow Simulation
DeepMind's new HydraNet model predicts hotspot formation with 92% accuracy. Early adopters report 40% fewer emergency shutdowns.
Real-World Success: Arizona's Solar Storage Project
When Salt River Project upgraded their 250MWh system last April, they faced a Monday morning quarterback situation. Their solution combined:
- Modular stainless steel pipes (Tier 3 material)
- Variable-diameter headers
- Distributed temperature sensors
The result? A 31% improvement in thermal uniformity. Their secret sauce? "We stopped treating pipelines as passive components," says lead engineer Maria González.
Material Selection Matrix (2023 Standards)
Material | Thermal Conductivity | Cost Index |
---|---|---|
Carbon Steel | 54 W/mK | 1.0 |
Stainless 316 | 16 W/mK | 2.3 |
Polymer Composite | 0.8 W/mK | 3.1 |
Future Trends: Where Pipeline Design Is Headed
As we approach Q4 2023, two developments are changing the game:
- Quantum Cooling Optimization: D-Wave's recent partnership with Siemens enables hyper-accurate fluid dynamics modeling
- Phase-Change Materials: MIT's microencapsulated paraffin beads maintain ±0.5°C for 72 hours without active cooling
Honestly, the field's moving so fast that yesterday's best practices are already looking sort of cheugy. But one thing's certain - smart pipeline design remains the unsung hero of energy storage safety.
Handwritten-style commentField Note: Always account for seismic activity in pipe routing. California's 2022 incident taught us that lesson the hard way.
Your Next Steps
Before finalizing designs, ask:
- Does our layout minimize 90° bends? (They cause 17% more turbulence)
- Have we stress-tested for -40°C to 65°C cycles?
- Are access points spaced ≤3 meters apart for maintenance?
With the global thermal management market projected to hit $22.3B by 2027 (per Frost & Sullivan), getting pipelines right isn't just engineering - it's economics.
Contact Us
Submit a solar project enquiry,Our solar experts will guide you in your solar journey.