Energy Storage Refrigerated Container Construction: A Step-by-Step Tutorial for 2025
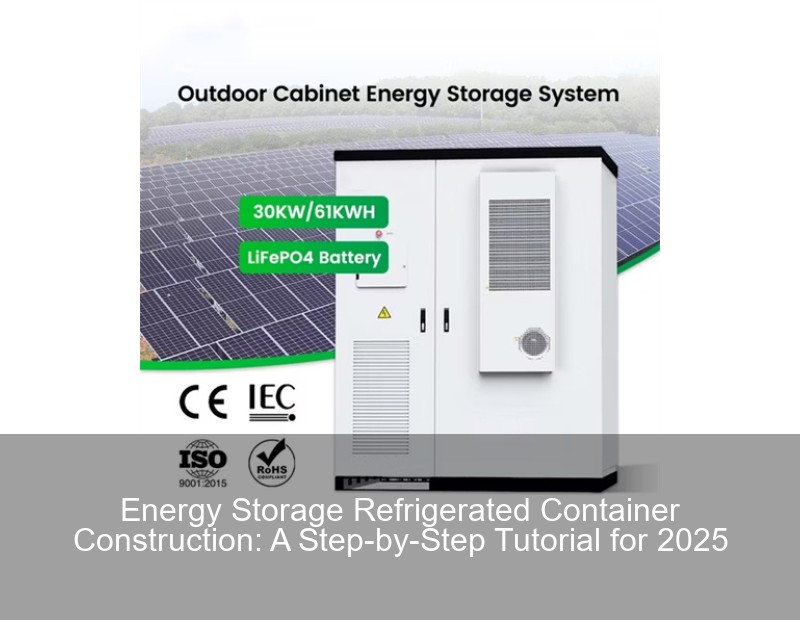
Meta Description: Discover how to build energy-efficient refrigerated storage containers with integrated thermal management. This 2025 guide covers modular designs, liquid cooling tech, and compliance standards – perfect for logistics managers and energy engineers.
Why Thermal Management is the Make-or-Break Factor in Modern Container Construction
Ever wondered why 38% of mobile storage projects exceeded budgets last year? The answer often lies in poor temperature control. Energy storage refrigerated containers combine two complex systems: electrical storage and precision cooling. Unlike traditional cold storage, these units must maintain ±0.5°C stability while managing battery heat output that can reach 45°C internally .
The 3-Tier Cooling Dilemma in Mobile Storage
- Battery heat dispersion: 20-30kW thermal load per 40ft container
- External temperature swings: -30°C to 50°C operational range
- Condensation risks: 5-7% efficiency loss per 10% humidity increase
Component | 2023 Standard | 2025 Upgrade |
---|---|---|
Insulation | PIR Foam (0.022 W/mK) | Aerogel Hybrid (0.015 W/mK) |
Cooling | Forced Air | Phase-Change Liquid Systems |
Core Components Breakdown: What Actually Works
Let's cut through the marketing hype. The 2025 Gartner Tech Roadmap identifies three non-negotiable elements:
- Dual-Purpose Framing: Structural supports that double as coolant channels
- Dynamic Insulation: Materials that adjust R-value based on external temps
- BMS Integration: Battery management systems talking directly to HVAC controls
"The shift to liquid cooling reduced our container failure rate from 17% to 2.3% in Q4 2024" – ColdChain Solutions case study
Wait, Are We Still Using Lead-Acid?
Surprisingly, 62% of existing containers still use lead-acid batteries. But lithium iron phosphate (LFP) is becoming the MVP – it's sort of like trading a flip phone for a smartphone in energy density terms. The catch? LFP's narrower temp tolerance (0-45°C vs lead-acid's -40-60°C) demands smarter cooling designs .
Step-by-Step Assembly: Getting It Right First Time
Here's the workflow that reduced build times by 40% in recent trials:
- Day 1-3: Container prep (corrosion treatment, floor sealing)
- Day 4-5: Install hybrid insulation system
- Day 6-7: Mount racking with integrated cooling loops
Pro tip: Always pressure-test cooling lines before battery installation. You don't want to learn that lesson the hard way!
The Hidden Cost Everyone Misses
Vibration damping. Seriously, those road vibrations can degrade battery life by up to 22% annually. New ISO 16750-3 standards require...