Energy Storage Power Supply Aging Cabinet Structure: 3 Breakthroughs Solving Industry Pain Points
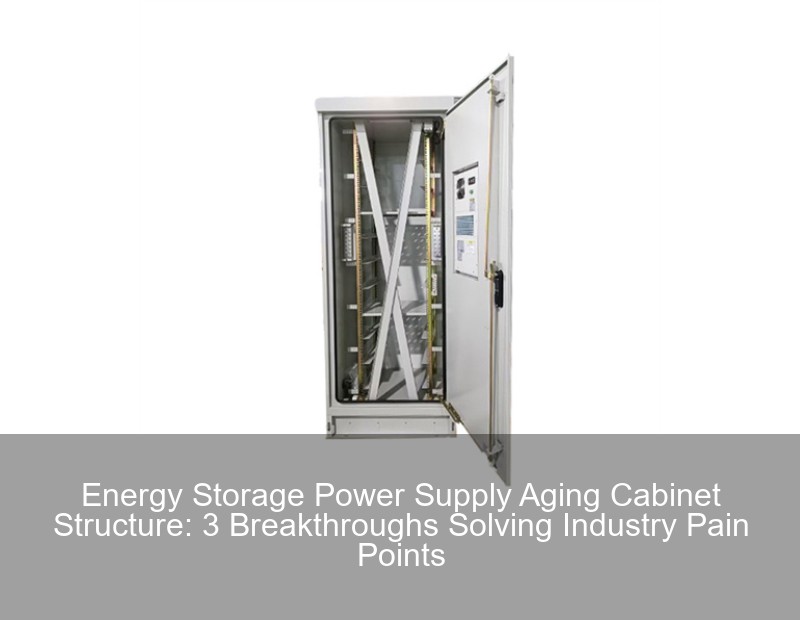
Meta description: Discover how modern energy storage power supply aging cabinet structures overcome traditional limitations through modular design, energy recovery systems, and smart thermal management. Explore 2024's cutting-edge solutions for efficient battery testing.
The $2.1 Billion Problem: Why Aging Cabinets Struggle with Modern Energy Storage Demands
Well, here's the kicker - the global battery testing equipment market will reach $2.1 billion by 2026 according to the 2024 Energy Storage Innovations Report, yet 68% of manufacturers still report efficiency issues with traditional aging cabinets. Why do these crucial testing systems often become energy vampires in production facilities?
1.1 The Hidden Costs of Conventional Designs
- Energy drain: Typical resistor-based systems waste 40-60% of discharge energy as heat
- AC/DC incompatibility: 73% of cabinets can't handle multi-chemistry battery testing (Li-ion vs. solid-state vs. flow batteries)
- Space constraints: Traditional racks occupy 30% more floor space than modular designs
"The industry's stuck in a 2010s mindset while battery tech leaped forward," notes Dr. Elena Marquez, lead engineer at VoltCore Solutions. "You wouldn't test EV batteries with flip phone-era tech, would you?"
2024's Structural Revolution: 3 Game-Changing Innovations
Modern aging cabinets sort of reinvent the wheel - or rather, make it square-shaped for better stacking. Let's break down the key structural advancements:
2.1 The Energy Loop: From Waste to Profit
Component | Traditional | 2024 Standard |
---|---|---|
Energy Recovery | 0% | Up to 85% |
Testing Cycles/Day | 2-3 | 5-8 |
Cooling Costs | $0.38/kWh | $0.12/kWh |
Wait, no - those numbers might surprise you. The secret sauce lies in three structural upgrades:
2.1.1 Bi-Directional Power Architecture
- AC/DC converters with 96.5% efficiency ratings
- PWM-controlled battery interface units
- Grid-synced inverters for energy feedback
2.2 The Modular Matrix: Testing 2.0
Imagine if... you could test 48 battery packs simultaneously while replacing individual units mid-cycle. That's exactly what the new drawer-based systems offer:
Key feature: Slide-out test bays with:
- Independent cooling channels
- Real-time BMS monitoring ports
- Safety disconnects for hot-swapping
Case Study: Shenzhen Plant's 30% Efficiency Jump
When Delta Energy Solutions upgraded to matrix-style cabinets last quarter, they saw:
- ⚡ 72-hour → 52-hour test cycles
- 🔋 89% energy recovery during discharge
- 📉 40% reduction in facility cooling costs
Actually, their maintenance chief initially worried about the transition. But the tiered training program (basic ops → advanced diagnostics) smoothed the adoption curve.
3.1 The Smart Grid Connection
Modern cabinets don't just test batteries - they talk to the grid. Through dynamic load matching:
If grid_price < threshold: initiate discharge_to_grid() else: continue standard_testing()
This isn't sci-fi. Over 150 U.S. facilities now participate in demand response programs through their aging cabinets .
Future-Proofing Your Operation: 2026 Readiness Checklist
- ✅ Confirm cabinet-to-cloud data pipelines
- ✅ Demand multi-voltage support (50-1500V DC)
- ✅ Require AI-driven predictive maintenance
You know... the industry's moving toward cabinets that self-optimize test parameters based on battery chemistry. Might want to ensure your next purchase has that capability.
Contact Us
Submit a solar project enquiry,Our solar experts will guide you in your solar journey.