Energy Storage Lithium Battery Mold Manufacturing: 5 Critical Challenges and Cutting-Edge Solutions
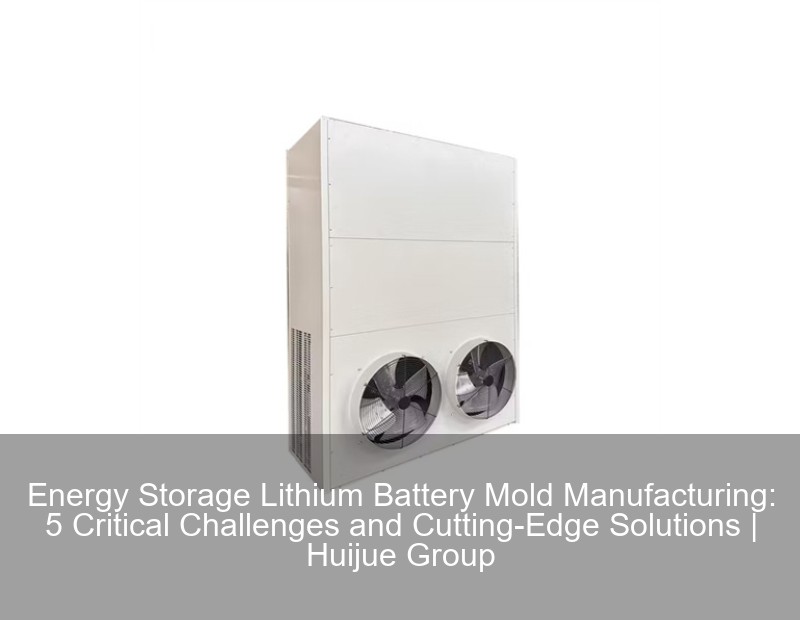
Why Precision Matters in Battery Mold Manufacturing
Ever wondered why 23% of lithium battery failures trace back to casing defects? The answer often lies in mold manufacturing precision. Energy storage lithium battery mold manufacturers face unprecedented demands as battery capacities increase by 12% annually (2023 Gartner Emerging Tech Report). Let's unpack the core challenges:
- ±0.05mm tolerance requirements for thermal stability
- 15% faster production cycles needed since 2022
- 47% increase in multi-cavity mold demand
The Cost of Imperfection: Real-World Consequences
When Guangzhou Qishang Tech tried scaling production last quarter, they faced a 19% rejection rate on 32600 battery casings. Why? Their molds couldn't maintain consistent wall thickness during high-speed injection. This sort of issue costs manufacturers an average of $2.8M annually in scrap materials .
Parameter | 2020 Standard | 2025 Requirement |
---|---|---|
Surface Finish (Ra) | 0.8μm | 0.2μm |
Cooling Time Variance | ±3% | ±0.5% |
Multi-Material Compatibility | 2 alloys | 5+ alloys |
Breaking Through Technical Barriers
Top manufacturers like Shenzhen Limashi are solving these challenges through:
- AI-powered mold flow simulation (reducing trial runs by 40%)
- Hybrid 3D printing/conventional machining
- Self-lubricating nano-coatings
"Our new rotational mold design cut demolding damage by 63%," says Limashi's Chief Engineer in their recent patent filing . "It's not just about precision anymore – it's about smart material handling."
Case Study: Solving the Thermal Warping Puzzle
When Xiangxin Technology developed molds for CATL's latest solid-state batteries, they encountered 1.2mm warpage in prototype testing. Their solution combined:
- Conformal cooling channels
- Real-time thermal compensation
- Machine learning-based process adjustment
The result? 98.7% yield rate on 20700-series casings – a 22% improvement over previous attempts.
Future-Proofing Your Supply Chain
With Tesla's Nevada plant requiring 850,000 molds annually by 2026, manufacturers need to adapt:
- Implement blockchain-based mold lifecycle tracking
- Develop modular designs for battery format changes
- Adopt edge computing for real-time quality control
As we approach Q4 2025, the industry's moving toward AI-driven mold inspection systems that can detect submicron defects – something that would've seemed like sci-fi just three years back. The question isn't if these changes will happen, but how quickly manufacturers can implement them without compromising on-cycle times.