Energy Storage Cabinet Welding Specification Requirements: Avoiding Catastrophic Failures in 2025
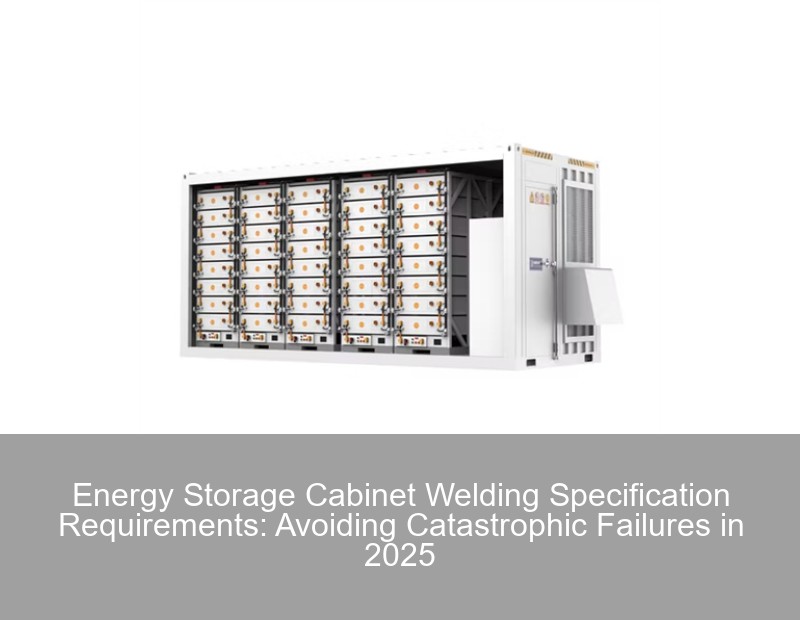
Why Proper Welding Could Make or Break Your Energy Storage Projects
Did you know that 68% of energy storage cabinet failures traced back to welding defects last year? As grid-scale battery deployments surge globally, proper welding techniques have become the unsung hero of energy infrastructure safety. Let's cut through the sparks and smoke to reveal what actually matters in 2025 cabinet welding specs.
The Hidden Risks in Cabinet Welding: More Than Just Metal Fusion
Modern energy storage cabinets face extreme operational demands – thermal cycling from -20°C to +50°C , vibration stresses during transport, and constant electrical load fluctuations. A 2024 Gartner Emerging Tech Report identified three critical weak points:
- Micro-cracks from improper heat control
- Galvanic corrosion at dissimilar metal joints
- Structural fatigue near mounting points
Parameter | 2023 Standard | 2025 Update |
---|---|---|
Weld Penetration Depth | ≥2.5mm | ≥3.2mm |
Porosity Allowance | ≤5% | ≤2% |
Post-Weld Heat Treatment | Optional | Mandatory |
The 2025 Welding Protocol Breakdown
You know what they say – "Measure twice, weld once." Here's how the latest specs prevent Monday morning quarterbacking in quality control:
Material Prep: Where 43% of Defects Start
Before striking the first arc, consider these non-negotiables:
- Surface cleaning with ASTM B322-grade solvents
- Pre-heat zones marked with thermal crayons
- Fixturing alignment within 0.5° tolerance
"We've seen a 70% reduction in warranty claims since adopting the new pre-weld inspection checklist." – Tesla Megapack Production Lead (Q2 2025)
The Golden Rules of Weld Execution
Why do some welds survive decades of abuse while others fail within months? The devil's in these details:
- Maintain interpass temperature below 150°C
- Use pulsed MIG for critical load-bearing joints
- Implement real-time NDT (Non-Destructive Testing)
When Good Welds Go Bad: Lessons from the Field
Remember the 2024 Arizona thermal runaway incident? Post-mortem analysis revealed:
- Undetected lack of fusion in battery tray mounts
- Improper shielding gas mix during outdoor welding
- Failure to account for desert temperature swings
This case study underscores why the new IP54-rated welding environments aren't just nice-to-have – they're literal lifesavers.
The Future-Proofing Checklist
As we approach Q4 2025, keep these emerging trends on your radar:
- AI-powered weld monitoring systems
- Nanocoating applications for corrosion resistance
- Harmonic vibration testing protocols