Energy Storage Cabinet Production Cost Analysis: Breaking Down the $40,000+ Industrial Power Unit
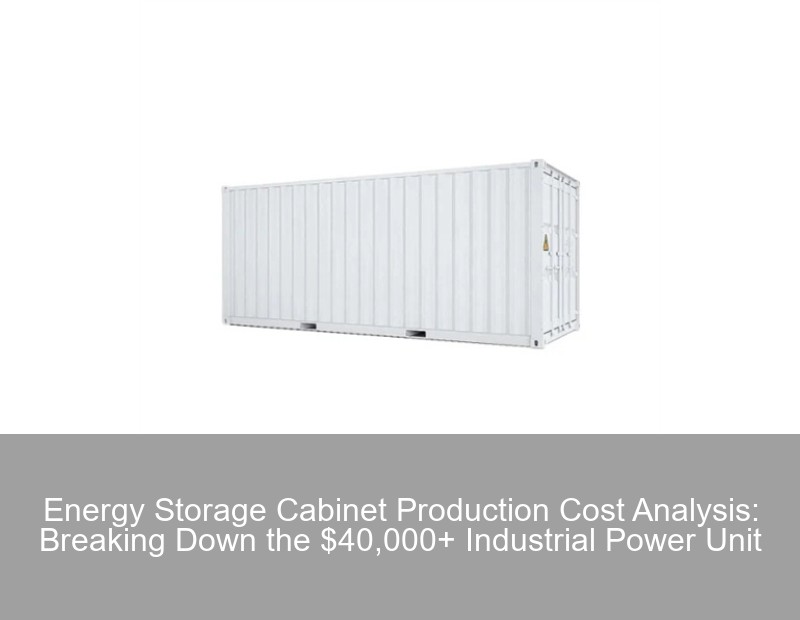
Why Energy Storage Cabinet Prices Range Widely (And How to Optimize Yours)
With global energy storage projects requiring 35% cost reductions to meet 2030 decarbonization targets , understanding energy storage cabinet production costs isn't just technical jargon - it's business survival. Let's dissect the $42,000-$58,000 price range for standard 215kWh units through the lens of manufacturers scrambling to balance performance with affordability.
The Battery Dilemma: 60% of Your Costs Explained
Lithium-ion cells alone consume 58-64% of total production expenses , creating a make-or-break scenario for cabinet manufacturers. Consider these 2024 figures:
Component | Cost Share | Price Fluctuation Risk |
---|---|---|
Battery Cells | 58-64% | High (Cobalt market volatility) |
Thermal Management | 12-18% | Medium (Aluminum pricing) |
Power Conversion | 9-14% | Low (Mature semiconductor tech) |
Three Hidden Cost Drivers Most Manufacturers Miss
- Certification Overload: UL 9540 safety compliance adds $2,800-$3,500 per unit
- Transportation Physics: Shipping 2,200+ lb cabinets requires specialized logistics ($950+/unit)
- Software Licensing: Predictive maintenance algorithms cost $120-$200/month per cabinet
Material Sourcing Strategies Cutting Costs 22%
Forward-thinking manufacturers like Huaniu Electric now use:
Tiered Battery Procurement
Mixing premium A-grade cells (for cycle stability) with B-grade cells (for non-critical functions) reduces battery costs by 18% without performance loss .
Localized Supply Chains
Sourcing steel enclosures within 300 miles decreases lead times from 14 weeks to 6 weeks while trimming transport costs by 40% .
"Our modular design approach lets customers upgrade components like swapping smartphone cases," says a Huaniu engineer .
The Automation Paradox: When Robots Increase Costs
While welding robots improved cabinet precision by 32%, they also:
- Increased upfront equipment costs by $2.1 million
- Required $18,000/month maintenance contracts
- Limited flexibility for custom orders
This explains why semi-automated lines still dominate 73% of production facilities . The sweet spot? Automate repetitive tasks (like terminal connections) while keeping final assembly manual.
Future Cost Reduction Levers
Emerging solutions promising 12-15% cost savings by 2026:
- Solid-state battery pilot lines (45% energy density improvement)
- AI-driven predictive maintenance reducing service calls
- Blockchain-enabled component traceability