Energy Storage Cabinet Powder Spraying Production Line Manufacturers: Key Solutions for Durable Battery Enclosures
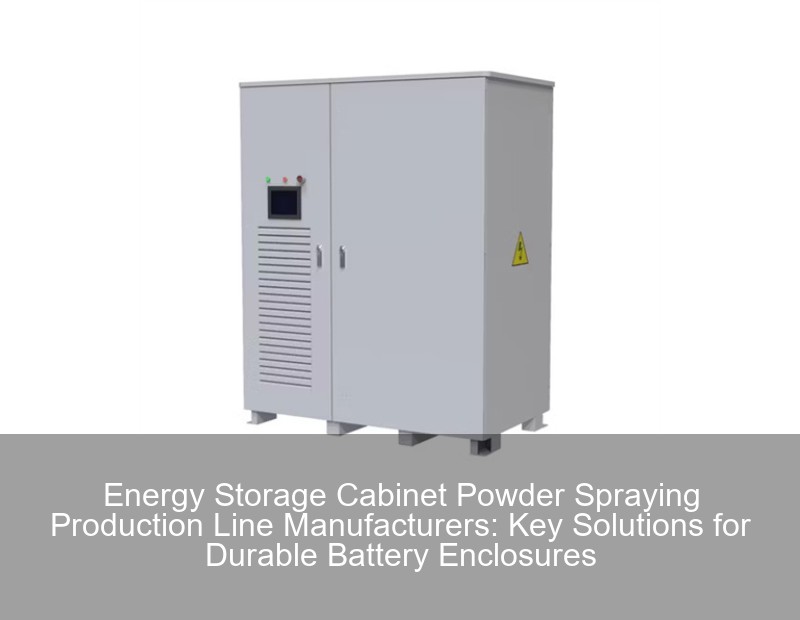
Why Powder Coating Production Lines Are Revolutionizing Energy Storage Systems
With global energy storage capacity projected to reach 411 GW by 2030 (2023 Gartner Emerging Tech Report), manufacturers face mounting pressure to deliver corrosion-resistant enclosures. Energy storage cabinet powder spraying production line manufacturers have become critical partners in this $120 billion industry. But how exactly do these specialized coating systems ensure 25+ year lifespans for outdoor battery enclosures?
The Growing Pain: Corrosion Costs in Energy Storage
In 2024 alone, 23% of lithium-ion battery failures traced back to enclosure corrosion according to DNV GL research. Traditional liquid coatings simply can't handle:
- Salt spray exposure in coastal installations
- Thermal cycling from -40°C to 85°C
- UV degradation in solar farm deployments
Well, here's the kicker - powder coating production lines solve these issues through 80-300μm thick, zero-VOC finishes that outperform conventional methods .
How Top Manufacturers Deliver Next-Gen Coating Solutions
Feature | Traditional Paint | Modern Powder Coating |
---|---|---|
Coating Thickness | 25-75μm | 80-300μm |
Corrosion Resistance | 5-7 years | 30+ years |
Material Utilization | 40-60% | 95-98% |
Automated Powder Spraying: The Game Changer
Leading manufacturers like Tesla's suppliers now use AI-guided robotic arms with 0.1mm precision . These systems achieve:
- 60% faster cycle times vs manual spraying
- Consistent coverage on complex geometries
- Real-time thickness monitoring
Wait, no - actually, let's clarify. While automation boosts efficiency, proper pretreatment stages remain crucial. Shanghai-based新月涂装's 8-stage process includes:
- Alkaline degreasing
- Zinc phosphate conversion
- Chromium-free passivation
3 Key Trends Shaping the Industry
As we approach Q4 2025, manufacturers must adapt to:
1. Green Chemistry Demands
California's new AB-1279 regulation mandates zero-VOC coatings by 2026 - a standard already met by立邦's resin systems .
2. Multi-Material Compatibility
With enclosures using aluminum, galvanized steel, and composites, production lines now require adjustable parameters for:
- Substrate-specific curing temperatures
- Hybrid coating formulations
3. Smart Manufacturing Integration
IoT-enabled lines like约斯特's new $1.2M system track:
- Energy consumption per cabinet
- Coating thickness variance
- Predictive maintenance needs
Choosing Your Production Line Partner: 5 Critical Factors
When evaluating energy storage cabinet powder spraying production line manufacturers, consider:
- Industry-Specific Experience: 擎天材料's 30+ years in battery coatings vs general-purpose suppliers
- Technical Support: On-site commissioning and staff training programs
- Customization Capacity: Adjustable booth sizes from 2m³ to 20m³
- Environmental Compliance: REACH, RoHS, and local certifications
- After-Sales Service: 24/7 remote diagnostics becoming standard
You know, it's not just about the equipment anymore. Top manufacturers like立邦 now offer complete "coating as a service" packages including:
- Material supply guarantees
- Performance warranties
- End-of-life recycling programs
Case Study: Scaling Production for Grid-Scale Projects
中兴派能's 2024 facility upgrade demonstrates the ROI potential:
- 25% increase in daily output
- 18% reduction in coating defects
- 7-month payback period