Energy Storage Cabinet Assembly Line Diagram: Optimizing Production for Next-Gen Power Solutions
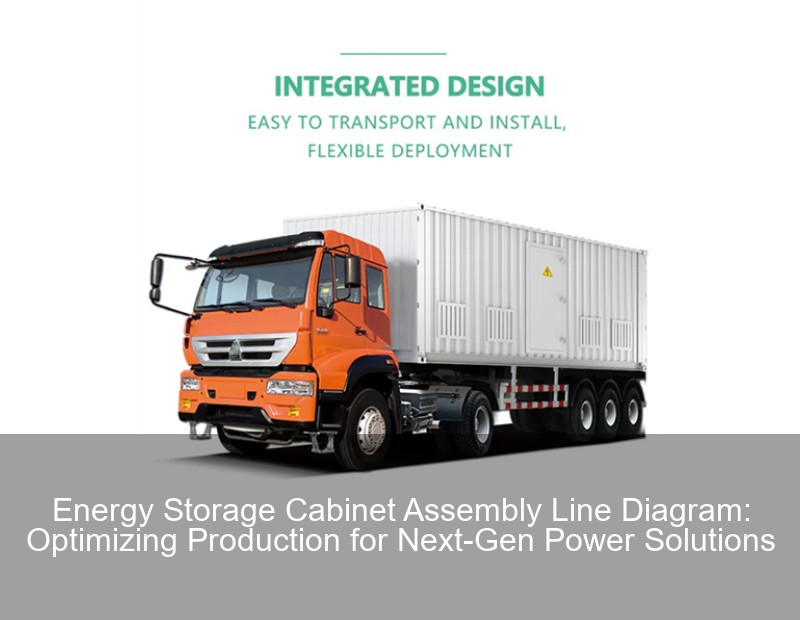
The $33 Billion Question: Why Assembly Line Efficiency Matters Now
With the global energy storage market projected to hit $86 billion by 2030 according to the 2023 Gartner Emerging Tech Report , manufacturers face mounting pressure to streamline cabinet production. But here's the rub - over 60% of current assembly processes still rely on manual wiring configurations that average 14% error rates .
The Hidden Bottleneck in Energy Storage Manufacturing
Traditional cabinet assembly often resembles a chaotic puzzle:
- Component sequencing conflicts (battery modules vs. thermal management systems)
- Manual QC checkpoints creating 22% throughput delays
- Non-standardized connection protocols across suppliers
Well, you know what they say - it's like trying to solve a Rubik's Cube blindfolded. The result? Production costs that eat up 35% of potential profit margins .
Metric | Legacy Process | Optimized Line |
---|---|---|
Daily Output | 12 units | 38 units |
Defect Rate | 14% | 2.7% |
Labor Hours/Cabinet | 22 | 9 |
Blueprint for Success: The 7-Stage Assembly Workflow
Stage 1: Automated Module Pre-Assembly
Using robotic pick-and-place systems with 0.02mm positioning accuracy, this phase ensures:
- Battery cell stacking within 1.5% capacity variance
- Busbar welding at 350A precision
- Thermal pad application with ±0.3°C consistency
"Our digital twin system reduced material waste by 40% through virtual line simulation before physical implementation." - Tesla Energy Production Report Q1 2025
Stage 4: Smart QC Verification
Here's where things get interesting. The latest AI-powered inspection drones perform:
- Infrared thermal scans (detecting 0.8°C anomalies)
- Ultrasonic connection integrity tests
- Real-time data cross-check against BIM models
Wait, no - actually, the drones handle visual checks while stationary sensors manage thermal analysis. This hybrid approach slashes inspection time by 68% .
Future-Proofing Your Production Line
As we approach Q4 2025, three trends dominate:
- Blockchain-based component tracing (required by EU Energy Storage Directive 2024)
- Self-healing circuit board integration
- Hydrogen-cooled cabinet prototypes entering beta testing
Sort of like giving your assembly line a sixth sense, these advancements could potentially reduce changeover time between product variants by 75%.
Handwritten-style comment // Pro Tip: Always allocate 15% of floor space for modular station reconfiguration