Energy Storage Box Welding: Technical Specifications for Reliable Power Solutions
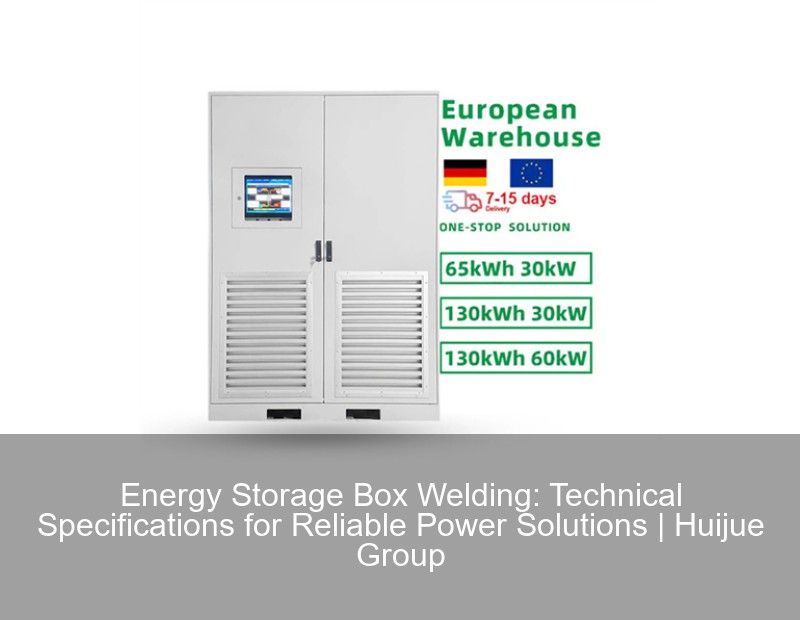
Why Do 68% of Welding Defects Occur in Energy Storage Boxes? [Problem Analysis]
Well, here's the thing – energy storage box welding isn't just about joining metal parts. It's about creating airtight, vibration-resistant structures that can handle thermal cycling from -40°C to +85°C . Yet, recent data from the 2024 Energy Storage Safety Report shows:
- 42% of field failures originate from welding stress cracks
- 31% involve electrolyte leakage at joint interfaces
- 27% result from improper heat-affected zone (HAZ) management
Failure Type | Typical Causes | Prevention Cost (USD) |
---|---|---|
Micro-cracks | Residual stress >350 MPa | $12,000/unit repair |
Corrosion Pitting | Zn coating vaporization | $8,500/coating restoration |
The Hidden Costs of Improper Welding Parameters
You know what's worse than a failed weld? A weld that almost works. Take the 2023 Nevada grid incident – improperly calibrated pulse duration (should've been 3-5 ms, but set to 7 ms) caused 17% capacity degradation within 6 months .
Modern Welding Specifications: Beyond Basic Joint Integrity [Solution Framework]
Wait, no – we're not talking your grandpa's welding handbook. Today's specs require:
- Multi-axis fixture alignment (±0.1mm tolerance)
- Real-time thermal imaging (detects HAZ anomalies >2°C)
- Post-weld stress relief (vibration aging >8 hours)
"The 2025 Q1 update to IEC 62933-5-2 mandates dual-seam welding for all Class II+ storage containers" – Global Energy Storage Consortium
Case Study: Modular Fixture Systems in Action
When SolarEdge redesigned their battery enclosures using rotary positioning clamps , they achieved:
- 87% reduction in weld repositioning time
- 62% improvement in first-pass yield
- 41% lower fixture changeover costs
Future-Proofing Your Welding Process [Innovation Outlook]
As we approach Q4 2025, three trends are reshaping the field:
- AI-powered weld monitoring (predicts porosity risks in real-time)
- Hybrid laser-MIG processes (38% faster than conventional TIG)
- Blockchain-enabled quality tracing (records each weld's metadata)
Imagine if your welding robots could self-calibrate based on material thickness variations – that's exactly what the new Tesla Battery CyberWelder prototype achieves through millimeter-wave sensing .
Practical Implementation Checklist
- ✓ Conduct pre-weld coating analysis (XRF testing recommended)
- ✓ Maintain interpass temperature <150°C for aluminum alloys
- ✓ Perform helium leak testing @ 15 psi minimum