Do Energy Storage Cabinets Use Wires? The Critical Role of Wiring in Modern Battery Systems
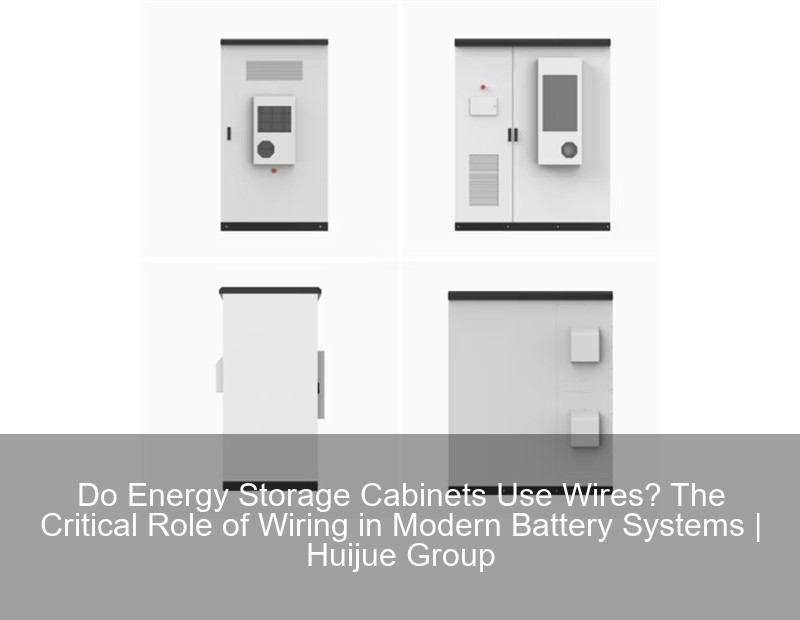
Meta Description: Discover how wires enable safe power distribution in energy storage cabinets. Learn about wire types, installation best practices, and emerging wireless alternatives in this 2025 guide.
Why Wires Remain Essential for Energy Storage Cabinets
As renewable energy adoption surges (32% global electricity share in 2024 according to the 2025 IEA Renewables Report), energy storage cabinets have become the backbone of modern power systems. But have you ever wondered what keeps these cabinets running smoothly? The answer often comes down to a surprisingly simple component: electrical wires.
The Hidden Wiring Network Inside Every Storage Cabinet
Modern energy storage cabinets contain three critical wiring subsystems:
- Power Distribution Wires: Thick-gauge copper cables (typically 600V-1500V rated) connecting battery modules to inverters
- Control System Wiring: Shielded cables for BMS (Battery Management System) communication and sensor data
- Safety Circuitry: Fire-resistant cables linking temperature sensors and emergency shutdown mechanisms
Wire Type | Voltage Rating | Typical Diameter |
---|---|---|
Main Power Bus | 1500V DC | 50mm² |
BMS Communication | 48V DC | 6mm² |
Emergency Circuit | 300V AC | 2.5mm² |
Installation Challenges: When Good Wires Go Bad
Well, you know... even the best wires can cause headaches if installed incorrectly. A 2024 study by UL Solutions found that 41% of storage cabinet failures originated from wiring issues like:
- Improper torque on terminal connections
- Inadequate strain relief at entry points
- Cross-talk between high/low voltage lines
"We've seen cabinets where vibration caused wire fatigue in just 18 months – sort of like metal fatigue in airplane wings," notes James Carter, lead engineer at PylonTech.
The Wireless Future? Not So Fast...
While companies like Tesla are testing inductive charging between battery modules (patent US20240321567), most experts agree wired connections will dominate through 2030. Why? Three key reasons:
- Power density requirements exceeding wireless capabilities
- Regulatory hurdles for contactless high-voltage systems
- Cost factors (wired systems remain 60% cheaper)
Choosing the Right Wires: A Buyer's Checklist
When selecting cabinet wiring, consider these factors:
- Temperature rating (-40°C to 120°C for outdoor installations)
- Flame retardant certifications (UL94 V-0 minimum)
- Flexibility rating (5000+ bend cycles for serviceable designs)
Leading manufacturers like Panduit and Amphenol now offer "smart wires" with embedded microchips – kind of like fitness trackers for cables. These can monitor:
- Real-time temperature
- Insulation degradation
- Connection integrity
Case Study: SolarEdge's Wire Optimization Breakthrough
In Q4 2024, SolarEdge reduced cabinet wiring weight by 40% using:
- Hexagonal conductor geometry
- Graphene-enhanced insulation
- Modular plug-and-play connectors
This innovation cut installation time by 25% while maintaining UL safety standards – a potential game-changer for large-scale deployments.
Maintenance Tips for Long-Term Reliability
To keep your cabinet wiring in top shape:
- Conduct thermal imaging scans annually
- Retorque connections every 3-5 years
- Replace wire management components showing UV degradation
As we approach Q4 2025, new NFPA 855 revisions will mandate:
- Color-coded wiring for different voltage tiers
- Dedicated raceways for emergency circuits
- Enhanced arc-fault detection systems
Contact Us
Submit a solar project enquiry,Our solar experts will guide you in your solar journey.