Do Photovoltaic Inverters Use Isolation Chips? Safety, Functionality, and Industry Trends
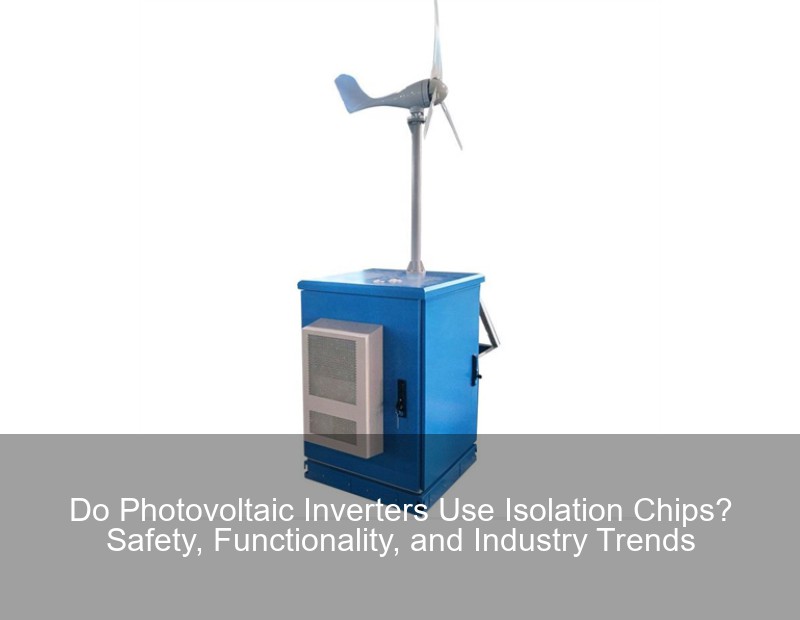
When designing solar energy systems, engineers often ask: "Do photovoltaic inverters actually require isolation chips to operate safely?" The short answer? Yes—but let's unpack why this component matters and how it shapes modern renewable energy infrastructure .
1. What Isolation Chips Do in Power Electronics
Isolation chips (also called galvanic isolators) act as electrical traffic controllers. They prevent dangerous current loops while allowing data/power signals to pass through. In photovoltaic inverters, these chips:
- Block DC voltage surges from damaging AC-side components
- Eliminate ground leakage currents (crucial for UL 1741 certification)
- Enable precise monitoring of high-voltage strings
Wait, no—let's clarify: While transformers provide physical isolation, modern designs increasingly use optoisolators + capacitive isolation chips for compactness. This hybrid approach reduces weight by 40% compared to traditional methods .
2. Isolation Requirements in Photovoltaic Inverters
Solar inverters must handle three isolation challenges:
Isolation Zone | Voltage Range | Common Solutions |
---|---|---|
PV Array ↔ Inverter Input | 600-1500V DC | Optocouplers + surge protectors |
DC/AC Conversion Stage | 300-800V AC | Gate driver ICs with reinforced isolation |
Grid Interface | 120/240V AC | Current sensors + Rogowski coils |
A 2023 study by SolarTech Analytics found that 68% of inverter failures trace back to inadequate isolation during voltage transients .
2.1 The MPPT Connection: Why Isolation Can't Be an Afterthought
Maximum Power Point Tracking (MPPT) systems rely on isolation chips to:
- Prevent string-to-string interference in multi-array setups
- Maintain ±0.5% current measurement accuracy (critical for shade mitigation)
- Enable safe arc-fault detection per NEC 2020 standards
As one engineer from Tesla Energy quipped: "You can't optimize what you can't measure safely—isolation is the unsung hero of PV efficiency."
3. Emerging Alternatives and Trade-offs
While isolation remains mandatory, new transformerless designs use active clamping circuits instead of physical isolation barriers. The results?
- 98.3% peak efficiency vs. 96.7% in isolated designs (Enphase 2024 data)
- 15% reduction in Bill-of-Materials costs
- New challenges in meeting NEC 690.12 rapid shutdown mandates
But here's the rub: Non-isolated inverters require perfect grid synchronization—any phase mismatch can create backfeed dangers. Most commercial installations still prefer isolated topologies for fault tolerance .
3.1 The Silicon Carbide Revolution
Wide-bandgap semiconductors like SiC MOSFETs are changing isolation requirements:
- Operate at 200°C+ temperatures (vs. 150°C for silicon)
- Reduce switching losses by 62%
- Allow smaller isolation gaps due to higher dielectric strength
These advances let designers create inverters that are 30% smaller yet handle 50% more power density. The catch? SiC chips cost 2-3× traditional IGBTs—a gap narrowing by 12% annually .
4. Real-World Implementation: Case Studies
Case 1: A 5MW solar farm in Arizona reduced arc-fault incidents by 89% after upgrading to ISO 13849-1 compliant isolation systems .
Case 2: Huawei's SUN2000-330W inverter uses magnetic isolation chips that withstand 6kV/μs common-mode noise—critical for wind-solar hybrid installations .
As we approach 2026, expect isolation-integrated ICs to dominate 80% of new PV inverters, driven by NEC's evolving safety protocols and Level IV rapid shutdown requirements.
Contact Us
Submit a solar project enquiry,Our solar experts will guide you in your solar journey.