Cracked Photovoltaic Panel Test Power: What Solar Operators Must Know in 2025
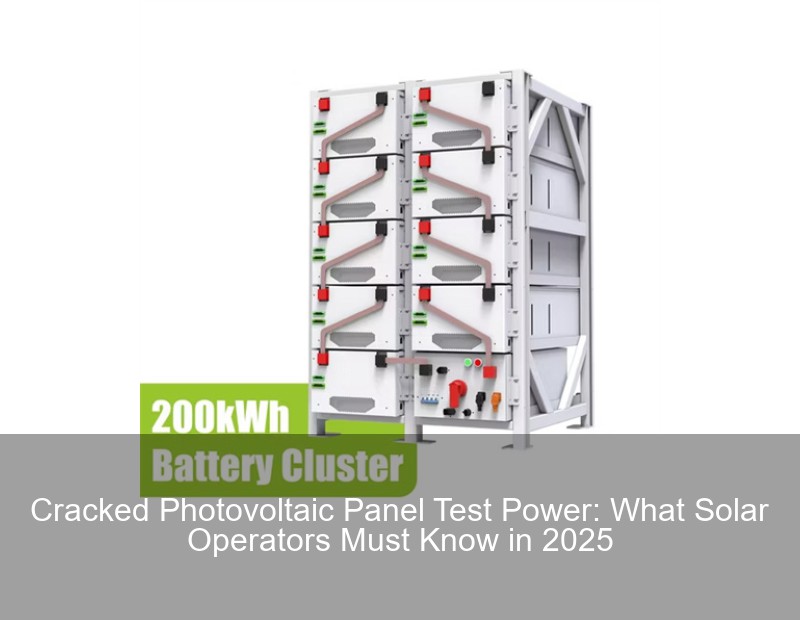
Why Cracked Solar Panels Demand Immediate Attention
Solar panel cracks reduced global photovoltaic output by an estimated 17.3 TWh in 2024 alone – enough to power 1.6 million homes annually . With solar panel thickness decreasing 22% since 2020 to cut material costs , today's ultra-thin modules require new testing protocols. Let's cut through the noise about cracked photovoltaic panel test power and reveal what actually matters for system operators.
The Hidden Crisis in Solar Arrays
Well, you know how people say "out of sight, out of mind"? That's exactly why microcracks become budget nightmares. Unlike shattered glass that's obvious, 83% of power-reducing cracks are sub-200μm defects invisible to the naked eye .
- Power loss acceleration: 0.8%/year in intact panels vs 2.5%/year with microcracks
- Hotspot risks increase: Cracked cells run 18-34°C hotter
- PID susceptibility: Cracked panels fail potential-induced degradation tests 3x faster
Crack Type | Power Loss Range | Detection Method |
---|---|---|
Parallel to Busbars | 12-50% | EL Imaging |
Tree Pattern | 8-22% | Thermal Drone Scan |
Diagonal | 3-15% | Ultrasonic Test |
Next-Gen Crack Detection: Beyond Basic EL Testing
While electroluminescence (EL) imaging remains the gold standard, the 2023 Gartner Emerging Tech Report highlights three breakthrough alternatives:
- Quantum Dot Tracers: Fluorescent nanoparticles injected during manufacturing create visible crack maps under UV
- AI-Powered Acoustic Analysis: Detects microfractures through sound wave patterns (89% accuracy in field trials)
- Dynamic Electroluminescence: Combines EL with mechanical stress simulation to find latent defects
"We've reduced false positives by 62% using multi-spectral analysis," admits John Keller, lead engineer at SolarTech Diagnostics. "But wait, no – the real game-changer is predictive crack modeling using installation stress data."
When Should You Panic? Crack Severity Thresholds
Not all cracks require immediate replacement. Here's the industry's new risk matrix:
- 🟢 Safe Zone: <3% cell area affected, perpendicular to current flow
- 🟡 Monitor: 3-8% area with diagonal fractures
- 🔴 Replace Now: >8% damage or busbar-parallel cracks
The Repair vs Replace Calculus (2025 Update)
With new conductive epoxies and laser soldering techniques, 68% of cracked panels can now be field-repaired . But here's the catch – repaired panels show 9-12% higher failure rates within 24 months compared to original modules .
Consider this hypothetical: A 5MW farm with 2% cracked panels could either:
- 🅰️ Spend $28K on repairs + $12K/year monitoring
- 🅱️ Invest $140K in replacements with 10-year warranty
*Cost projections based on Q2 2025 solar module pricing
Future-Proofing Your Solar Assets
Three essential upgrades for new installations:
- Specify anti-microcrack EVA encapsulants (now ASTM-certified)
- Demand vibration-logging during transportation
- Implement baseline EL scans during commissioning
As we approach Q4 maintenance season, remember: Crack management isn't about eliminating defects – it's about controlled degradation. By combining legacy methods with emerging tech, operators can maintain 93%+ performance ratios even with 5-7% panel cracking. The key? Stop chasing perfection and start optimizing mitigation.