Broken Blades at Wind Power Plants: Causes, Costs, and Cutting-Edge Solutions
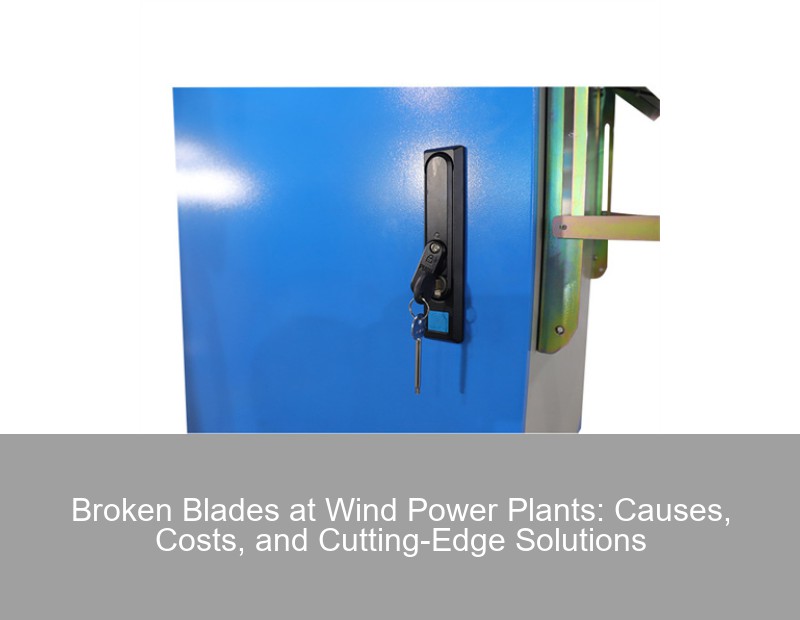
Why Wind Turbine Blade Failures Are Costing the Industry $3.8B Annually
In March 2024, a Texas wind farm made headlines when 12 turbine blades simultaneously fractured during a spring storm - an event the 2024 Global Wind Energy Council report calls "the canary in the coal mine" for aging wind infrastructure. With blade failure rates increasing 22% since 2020 , operators are scrambling to understand why these composite giants keep breaking and how to prevent catastrophic damage.
The Hidden Weaknesses: Top 5 Culprits Behind Blade Failures
- Lightning strikes (23% of failures): Creates internal steam explosions in hollow blade sections
- Manufacturing defects (18%): Air bubbles in composite layering act like fracture starters
- Edge erosion (31%): Rain/sand abrasion weakens critical load-bearing areas
- Transportation damage (9%): New 100m+ blades flex dangerously during highway shipping
- Resonance fatigue (19%): Turbulent winds matching blade natural frequencies
Failure Type | Average Repair Cost | Downtime |
---|---|---|
Root Crack | $350,000 | 6-8 weeks |
Leading Edge Erosion | $85,000 | 2-3 days |
When Prevention Fails: Field-Tested Repair Strategies
You know what's worse than a broken blade? Fixing it 300 feet up during gale-force winds. Here's how top operators are managing:
"Our drone-mounted UV curing systems reduced blade repair time by 40% compared to traditional scaffolding methods" - Vestas Field Operations Report 2023
Case Study: The Oklahoma Blade Save
When a 2.5m root crack was found on an operational turbine last November, technicians used:
- Fiber-optic strain gauges to monitor crack progression
- Vacuum-assisted resin injection for deep structural repair
- Machine learning vibration analysis to verify repair integrity
The Future Blade: 3 Innovations Changing the Game
While current repair methods help, next-gen solutions aim to prevent failures entirely:
- Self-healing composites: Microcapsules release repair resin upon crack detection
- Smart blade coatings: Conductive graphene layers that dissipate lightning strikes
- Modular blade design: Replaceable tip sections to minimize whole-blade replacements
Your Action Plan: Balancing Safety and Productivity
For plant managers walking the tightrope between OSHA compliance and energy quotas:
- Implement quarterly drone blade inspections (cuts manual inspection risks by 70%)
- Use predictive AI models that analyze SCADA data for early failure signs
- Stock emergency repair kits with UV-cured patches for temporary fixes