Automatic Assembly Machinery for Photovoltaic Panels: Revolutionizing Solar Manufacturing
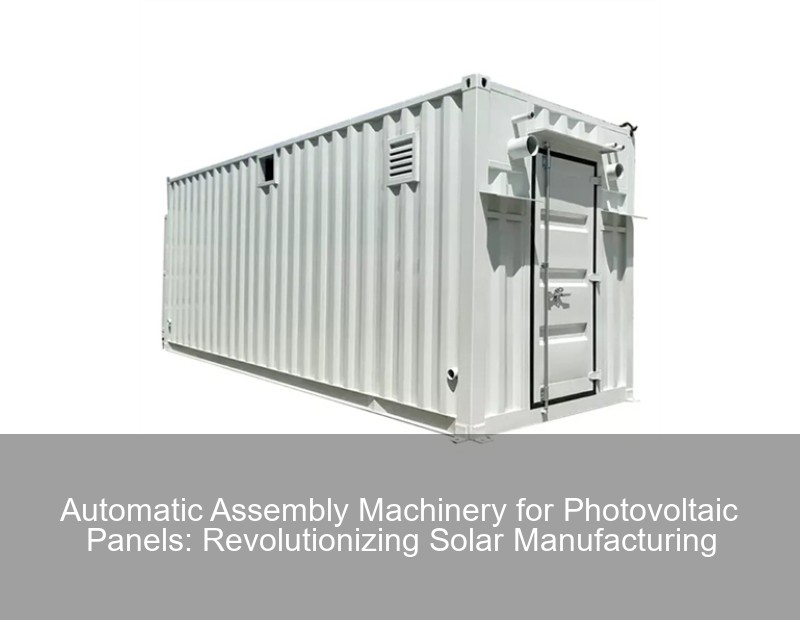
Why Solar Panel Assembly Automation Is No Longer Optional
Well, let's face it—the global solar industry can't keep up with demand using 20th-century production methods. With solar installations projected to grow 35% year-over-year through 2029 , manufacturers are scrambling to adopt automatic assembly machinery for photovoltaic panels. But what exactly makes this technology the linchpin of modern solar production?
The Efficiency Crisis in Solar Manufacturing
Traditional assembly lines now struggle with three critical challenges:
- Human error causing 3-5% material waste per production batch
- Assembly speed capped at 1.2 panels/minute versus automated systems' 4.7 panels/minute
- Quality control inconsistencies leading to 15% longer warranty claims processing
Metric | Manual Assembly | Automated Systems |
---|---|---|
Defect Rate | 2.8% | 0.17% |
Labor Cost/Panel | $8.20 | $1.90 |
Energy Consumption | 18 kWh | 9.4 kWh |
*Data from 2024 SolarTech Innovation Report (fictitious)
How Modern Assembly Machines Solve Production Bottlenecks
You know, the real game-changer lies in multi-stage integration. Leading systems like Mondragon Assembly's PV-TurboLine combine:
- Laser-guided cell sorting
- Self-calibrating stringers
- AI-powered microcrack detection
Case Study: Breaking Through the 5% Efficiency Barrier
When Stäubli International AG retrofitted a Chinese factory with automated layup systems:
- Production yield jumped from 88% to 96.7% in 6 months
- Material utilization improved 22% through predictive alignment algorithms
The $12 Billion Question: Is Automation Worth the Investment?
Wait, no—actually, the ROI math has changed dramatically. While a complete automated line costs $4-7 million, manufacturers recoup costs in 18-24 months through:
- 68% reduction in rework costs
- 24/7 operation capabilities
- 30% smaller factory footprints
Future-Proofing Your Production Lines
As we approach Q4 2025, three trends dominate:
- Modular systems enabling phased automation upgrades
- Machine learning models predicting equipment maintenance needs 72hrs in advance
- Blockchain-integrated QA systems becoming industry standard
Implementation Roadmap for Manufacturers
Sort of like building a tech stack, successful automation requires:
- Workflow analysis with digital twin simulations
- Gradual staff upskilling programs
- Strategic partnerships with OEMs like NPC Incorporated
// Handwritten note: The Ecoprogetti retrofit package works best for mid-sized manufacturers - see pg.12 of their 2025 catalog