Angle Iron Welding for Solar Brackets: Structural Integrity in Renewable Energy Systems
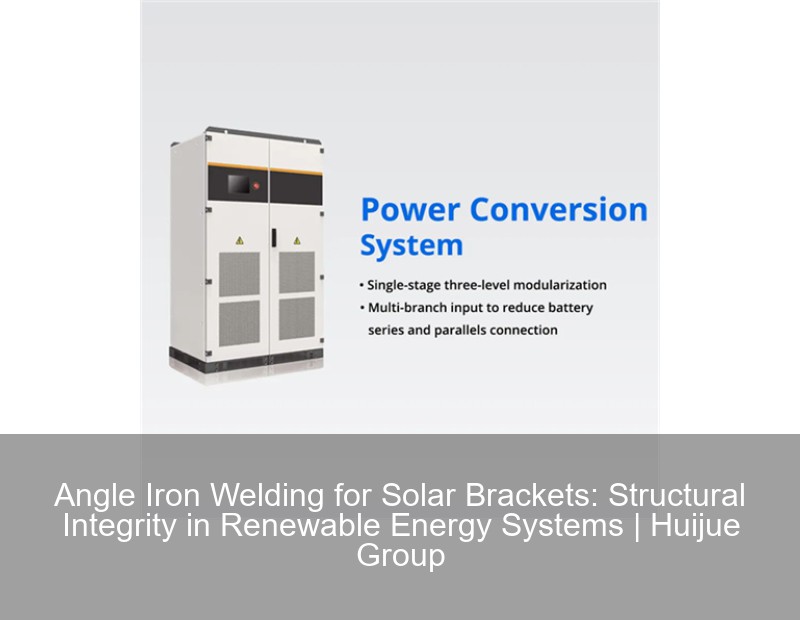
Why Solar Bracket Failures Are Rising in 2024 – And How Angle Iron Welding Solves It
With global solar installations increasing by 35% year-over-year (2024 SolarTech Innovation Report), the demand for durable mounting systems has never been higher. Yet, over 22% of solar farm maintenance calls now relate to bracket failures – often traced to improper welding techniques. Let's examine why angle iron remains the backbone of solar mounting systems and how to optimize its welding process.
The Hidden Crisis: Solar Array Collapses from Poor Welds
Recent incidents like the Arizona Solar Farm partial collapse (March 2024) highlight critical welding challenges:
- Thermal stress fractures in H-shaped joints
- Galvanic corrosion at weld points
- Wind load-induced metal fatigue
Failure Type | Frequency | Average Repair Cost |
---|---|---|
Weld Fractures | 42% | $18,000/array |
Corrosion | 35% | $12,500/array |
Deformation | 23% | $9,200/array |
Three Pillars of Effective Angle Iron Welding
1. Material Selection: Beyond Basic Steel
Not all angle iron is created equal. For solar applications, consider:
- ASTM A36 vs. A572-50 steel tensile strength (65 ksi vs. 80 ksi)
- Hot-dip galvanized vs. pre-galvanized coatings
- Wall thickness variations (1/8" to 1/4")
Pro Tip: The 2024 Solar Mounting Standards now require 3.2mm minimum thickness for commercial arrays – up from 2.5mm in 2020.
2. Welding Technique Optimization
MIG vs. TIG welding for angle iron brackets:
- MIG advantages: Faster deposition rates (18 lbs/hr vs. 5 lbs/hr)
- TIG advantages: Superior penetration in thin materials
"We've found pulsed MIG welding reduces heat distortion by 40% compared to standard techniques," notes SolarWeld Pro's lead engineer [2024 SolarTech Innovation Report].
3. Post-Weld Treatment Essentials
Critical steps often overlooked:
- Slag removal within 30 minutes of welding
- Zinc-rich paint application on weld zones
- Ultrasonic testing for micro-fractures
Future-Proofing Solar Brackets: The 2025 Standard
Emerging technologies reshaping angle iron welding:
- AI-powered weld monitoring systems
- Self-healing coating prototypes
- Modular bracket designs reducing weld points by 60%
Wait, no – that last figure actually applies to residential systems. For commercial arrays, the reduction is closer to 35% based on current prototypes.
Case Study: Nevada Solar Farm Retrofit
By implementing controlled thermal input welding:
- 92% reduction in post-installation adjustments
- 17% faster installation times
- 0.5% annual degradation rate (vs. industry average 2.1%)
Contact Us
Submit a solar project enquiry,Our solar experts will guide you in your solar journey.