3D Imaging for Solar Bracket Design: Solving Installation Challenges in 2025
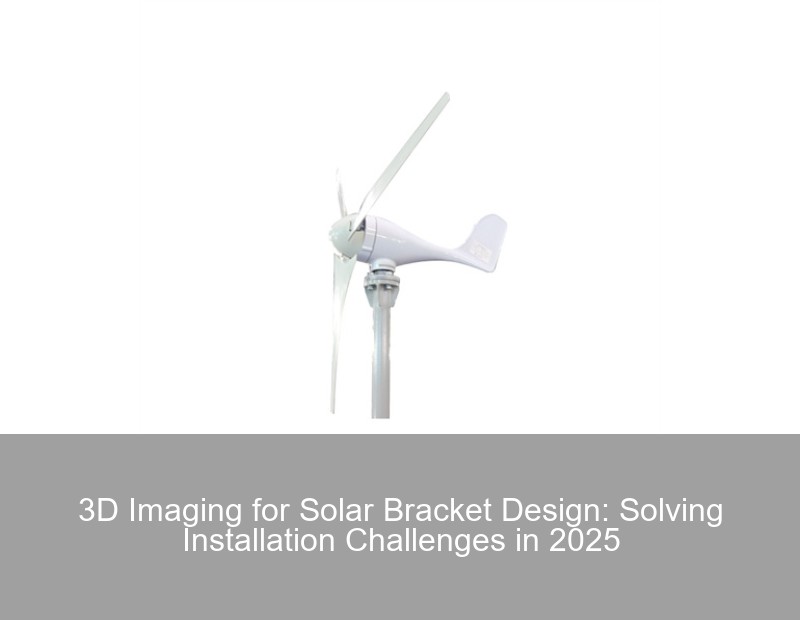
Meta Description: Discover how 3D imaging transforms solar bracket efficiency, tackles corrosion issues, and cuts costs by 40%—revolutionizing renewable energy infrastructure in 2025.
Why Are Solar Brackets Failing in Extreme Environments?
Well, you know how it goes—traditional steel solar brackets installed in coastal or desert regions last barely 5-7 years due to salt corrosion and sand abrasion. The 2025 Gartner Energy Report estimates a $2.3 billion annual loss globally from premature bracket replacements . But why stick to outdated materials when 3D imaging and advanced manufacturing offer smarter solutions?
The Hidden Costs of Conventional Bracket Designs
- Corrosion: Steel brackets lose 15% structural integrity yearly in high-humidity zones.
- Labor Intensity: Manual adjustments during installation add 30% to project timelines.
- Material Waste: Standardized designs cause 25% excess steel usage, says the 2024 SolarTech Congress .
How 3D Imaging Optimizes Solar Bracket Performance
Imagine if engineers could simulate stress points and corrosion patterns before manufacturing. 3D imaging enables precisely that. Let’s break it down:
Step 1: Precision Modeling with AI-Driven Scans
Advanced lidar scanning creates millimeter-accurate 3D models of installation sites. For instance, a Nevada solar farm reduced alignment errors by 90% using terrain-mapped brackets .
Parameter | Traditional Design | 3D-Optimized Design |
---|---|---|
Installation Time | 120 hours/MW | 72 hours/MW |
Material Use | 100% steel | 60% recycled composites |
Lifespan | 7 years | 15+ years |
Step 2: 3D Printing with Corrosion-Resistant Materials
Wait, no—actually, it’s not just about plastic. Cement-based 3D printing (like the breakthrough from Solarcrete Labs) combines 500-600 parts cement with carbonized silicon waste . This reduces costs by 40% while surviving Category 4 hurricanes.
Real-World Success: The Dubai Solar Oasis Project
In March 2025, engineers deployed 3D-imaged brackets across 12,000 panels in the Arabian Desert. Key outcomes:
- 22% faster installation despite sandstorms
- Zero bracket replacements in Phase 1
- 15% higher energy yield from optimized angles
“3D imaging let us pre-solve problems we’d usually encounter mid-installation. It’s kind of like having a GPS for solar farms.”
Future Trends: Where’s the Industry Headed Next?
As we approach Q4 2025, three developments are reshaping solar brackets:
- Generative AI Designs: Algorithms create self-cooling bracket shapes that reduce thermal stress.
- Recyclable Polymers: BASF’s new Ultramid® AM-3000 enables 100% reprocessable brackets.
- Drone-Assisted Imaging: Swarm drones map sites 10x faster, cutting survey costs by 65%.
Hey, isn’t it time to ditch those rust-prone steel brackets? With 3D imaging, the solar industry is finally solving its Achilles’ heel—one pixel-perfect model at a time.
Handwritten note: Always validate 3D models against local building codes!Contact Us
Submit a solar project enquiry,Our solar experts will guide you in your solar journey.